 |
Z軸についてはナットにスリ割を入れナット自体のバックラッシュを詰めたのだが締め過ぎると、どうしても重たくなりF値(移動速度)が上がりません。また、すぐガタが大きくなってしまうので、安定した精度維持と総合的な切削時間短縮の為にボールネジに換装する事にしました。 |
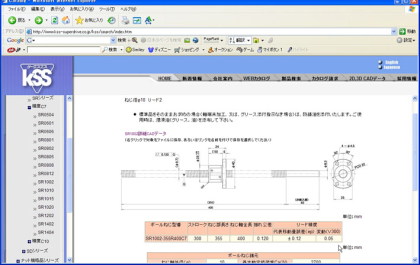 |
まずは使用するボールねじの寸法とCADデーターをWebから入手します。
サイズはオリジナルの台形ネジに合わせてΦ10mmのピッチ(リード) 2.0mmを使用しました。
小径の小リードが低価格なKSSボールネジを使います。
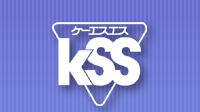
|
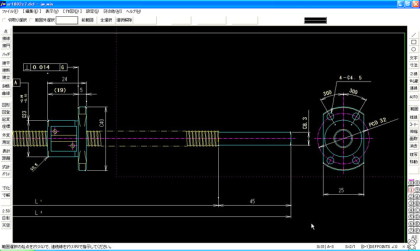 |
ダウンロードしたCADデーターからナット取り付けブラケットを検討します。
台形ネジと違いナット部分が大きいので寸法的な制約がありますので従来は円筒部分で固定し寸法を出すべきなのですがフランジ表面に角形のプレートを取りつけ固定する事にします。 |
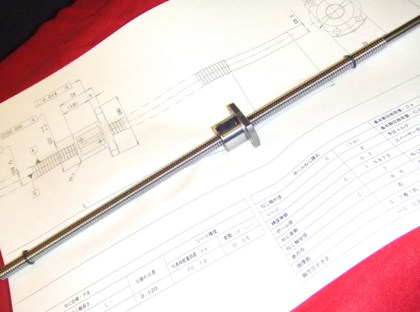 |
ボールネジ1式です。
ここで問題なのはナットを付けたままネジの端面を都合の良いように旋盤加工ができるかと言う事です。
リテーナー無しのナットのためネジからナットを外すと玉が落ち二度と組み立たなくなり御釈迦です。
長さは充分過ぎるくらい長いので切断しますが表面に焼き(58〜62HRC)が入っていますのでバンドソーが使えずサンダーで切断となります。 (ーー;)
後々の事を考えて切断端面はきれいに仕上げておきます。 |
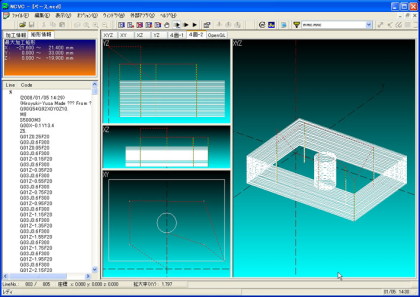 |
mini-CNC本体を分解する前に加工精度の必要なブラケット等の部品を事前にmini-CNCで製作しておきます。
左はボールねじのナット固定用ブラケットです。 |
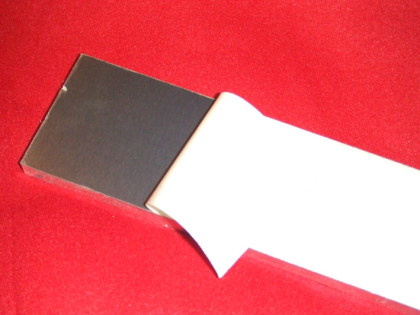 |
部品類は強度等を考慮して手持ちの半端材t=10mmの#2000高力のアルミ合金から削りだす事にします。 |
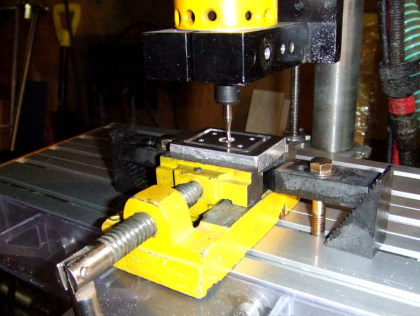 |
写真撮影のためバキュームとエァー・ブローのアタッチメントを外しての加工とします。
10mm厚の抜きになりますので刃長を考えてΦ4.0のロング・リーチ・エンドミルを使用します。 |
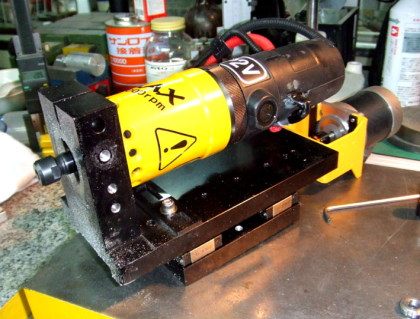 |
必要部品の切削が終わりましたので、Z軸周りを取り外します。 |
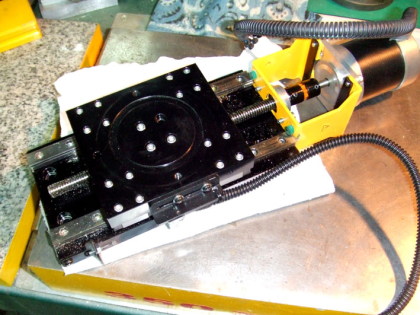 |
既設の外観です。 |
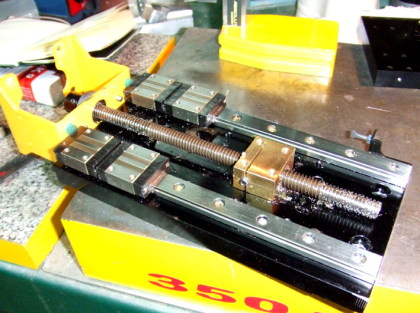 |
既設はこの様になっています。
リニアウェイをレールから外してしまわないように充分気を付けての分解です。
結構、切削屑等で汚れています。
やはりワイパーが無いと駄目かな
(ーー;)
いつも締め付けて(与圧)使っていたせいかネジにナットの真鍮色がうつっています。
いわゆるナットが減ったって事・・・? |
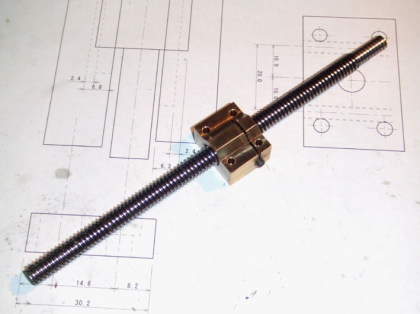 |
取り外した台形ネジです。
追加工でナットにスリ割を入れてセットスクリューで押してバックラッシュを殺すようにしているのが見えますが・・・・・・・・。
何かと (ーー;) ・・・です。 |
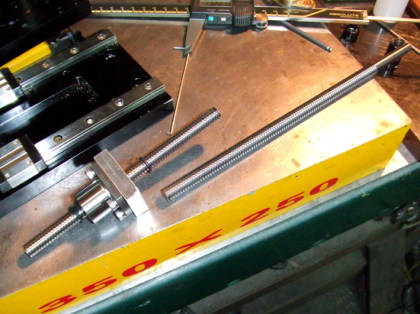 |
ここが重要です。
ボールねじの軸端面加工のためにナット自体を切り捨てる方に移動させてナットが脱落しないように前後にOリングを掛けて、必要寸法でネジを切断し切断端面を整えておきます。
これでネジの軸端面の加工が旋盤で自由にできるようになりました。 |
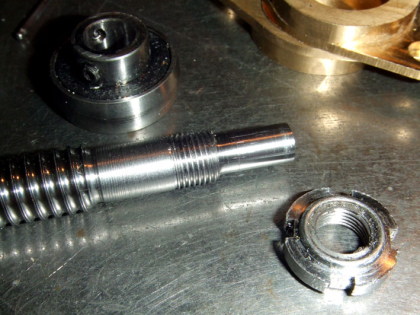 |
軸端の加工をします。
ベアリングの穴径に合わせてシャフト外径を調整切削し、次にベアリング・ナット用の雄ネジを切ります。
ネジはスラスト・ベアリング等と違い平行度は、それ程、精度が必要ないのでダイスでもOKです。
軸受けはピロユニットのベアリングのみを専用ケースで挟み込みM8のベアリングナットで締め込む事にします。 |
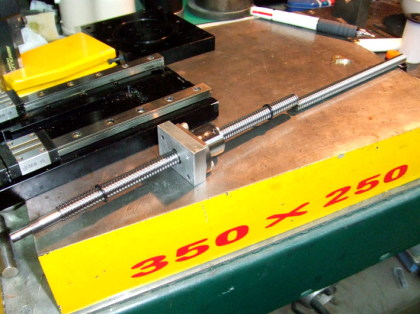 |
ナットを移動させます。
不要部分の切捨てる方のネジに取り付けておいた、ナットを加工済みのネジの方に移します。
既に整えておいたネジの端面同士をネジ山を合わせて瞬間接着剤で固定し1本にして慎重に回転させ使用する方のネジに移し終わったらナットの両側にOリングを掛けて次に接着部分をポキっと折れば完成です。 |
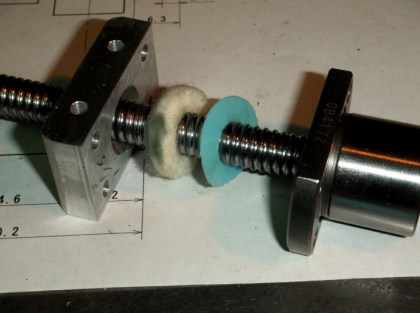 |
シールが付いていませんのでフエルトにグリスを沁み込ませてワイパーとするのですが、フエルトの繊維を噛み込んでしまうとNGなのでナット側にポルエチレン・シートから打ち抜いたシートを入れておきます。
固定用のブラケットで挟み込んでワイパー等を固定します。 |
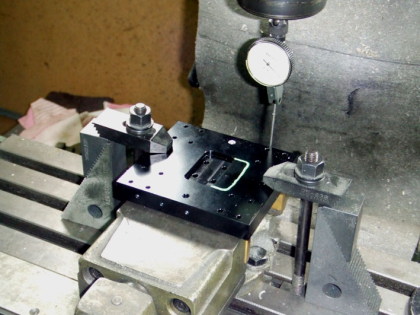 |
ベース等の追加工です。
ネジの中心を合わせるためにナット側のベースを2.4mm深く掘り込みます。
この辺の寸法は精度に大きく影響しますので慎重に芯だしを行いフライスでエンドミルを使い切削します。 |
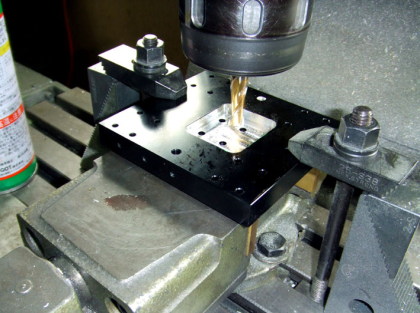 |
Myフライス盤で実際の切削をおこないます。 |
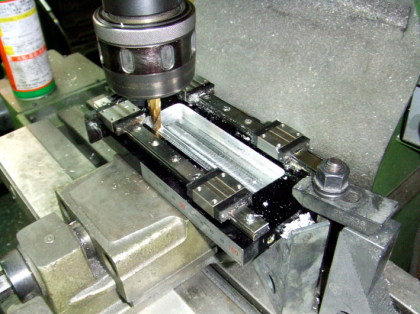 |
ベース等の追加工です。
ナットが大きくなって干渉してしまう部分を切削しますが、ここも既設から2.4mm掘り下げればOKのようです。
左画像では分かりにくいのですが切削の振動でリニアウェイがレールから脱落しないようにレール固定用ボルトの両端を緩め頭を出しておきストッパーとしておきます。
|
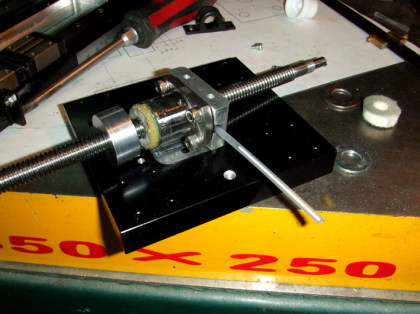 |
ナットの仮組です。
ナットの反対側にもワイパーを組み込み小型化の為に穴あきカップを作り被せます。
写真手前に伸びているチューブは給油用で一般的なケミカル用品に添付されているノズルを流用します。
(スプレー・グリスに、そのまま接続できるように) |
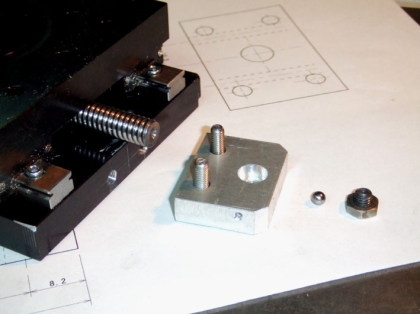 |
モーター側のベアリング一個で支持してもベアリング自体の公差でバックラッシュが出来てしまいますので、ボールねじのモーターと反対側の端面にR2.5のボール・エンドミルで窪みを作り、Φ5.0mmのスチール・ボールを返してM6のセット・スクリューの先端の窪みでネジを押し上げてドライブ側のベアリングに与圧をかけてバックラッシュを詰めれるようにします。
ホルダー側面の小穴はボールへのグリス供給用の穴です。
|
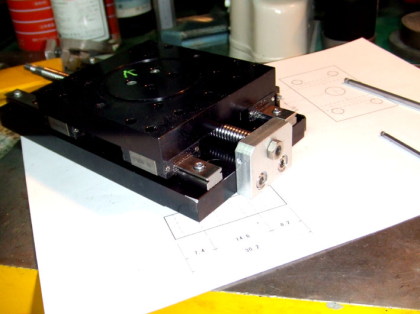 |
上を組み付けたところです。
調整後セット・スクリューにはM6の薄ナットをかけロックしておくことにします。
この段階での調整は、タップリボールにグリスを塗布しボールねじを指で回してみて重たくなる、ちょっと手前位で止めてロックしておきます。
本体に組み付け後、バックラッシュ計測後、満足な値が得られなければ再度、追い込む事にします。 |
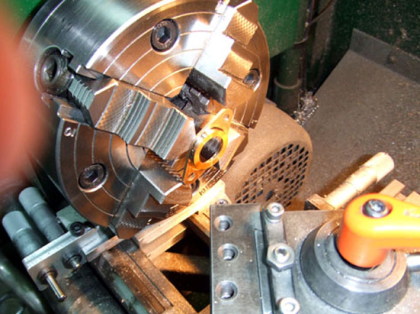 |
mini-CNCで荒取りしたベアリングケースの仕上げ加工を4つ爪チャックに挟んで行います。 |
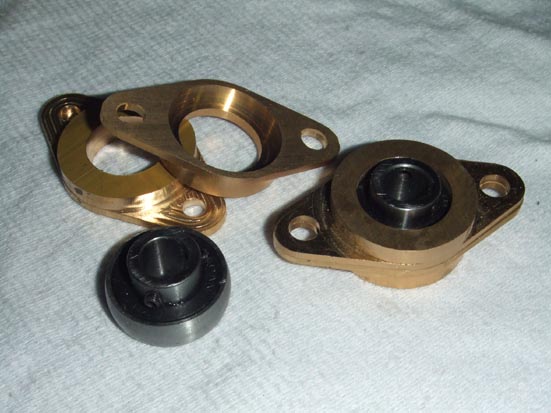 |
完成した二つ割ベアリング・ケースです。
材質は真鍮です。
ベアリングはスラスト専用ではなくラジアル荷重向けなのでスラスト方向には、ソコソコのガタがある事は仕方ないので、上に記載した方法でベアリングに与圧をかけてスラスト方向の遊び(ガタ/公差)を殺します。 |
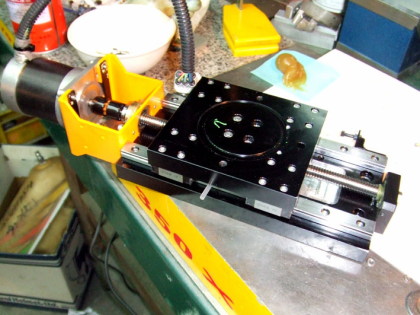 |
完成組み立てをおこないます。
給油用チューブが見えます。 |
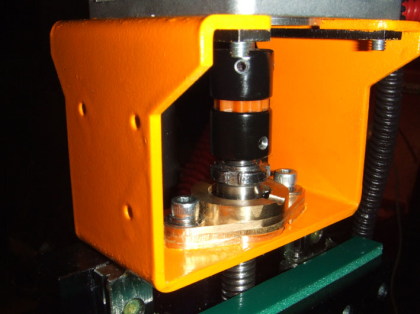 |
軸受け部分です。
ベアリング・ケース上面の半R溝はベアリングの軸固定用のセットスクリューを回す為に六角レンチが入りやすいように追加工します。 |
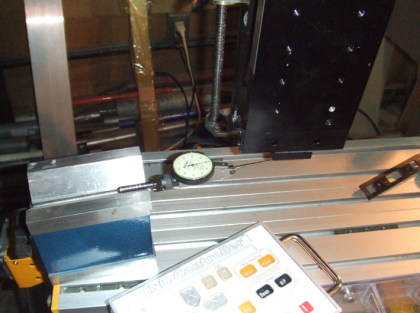 |
いよいよ本体にZ軸周りを取り付けての精度確認です。
一般的なやり方だと思いますが私の場合は、下記要領でやります。
@テストインジケーターをテーブル側に固定し(マグネットVブロックで取りつけシャフトを吸磁させます)アームをZ軸の異動部分に当てます。
AMachのJog Modeで0.1位のステップで下方移動させ適当なところで停止させテスト・インジケーターの目盛りを記録(記憶)します。
BMachのZ軸カウンターを0セットします。
次にMachのJog Modeで0.001程度のステップで上方にチョン、チョンと送りをかけテスト・インジケーターの針の触れに注視します。
Cテスト・インジケーターの針が振れたところで送りを止めMachのZ軸のカウンターを読み取ります。
@〜Cを下限、中、上限で下方送り、上方送りの6ポジションで計測します。
多分バックラッシュの測定は、これでOKだと思います。但し、代表移動量誤差については、別の方法が必要ですね。 |
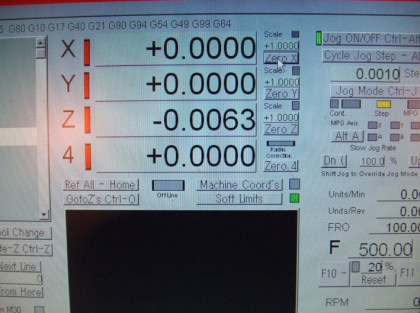 |
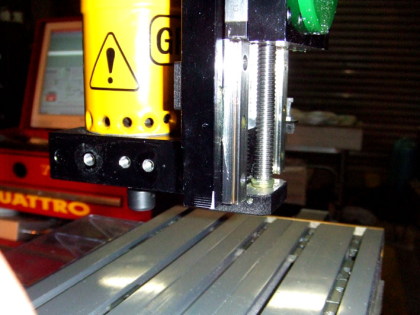 |
ねじ端面のスチール・ボールの押しが利いて調整後のZ軸のバックラッシュは左上画像出見えるように 0.0063mmでした。
あくまでもステッピング・モーターが理論通り動いての事ですので後は切削&測定のカット・アンド・トライで調整ですね。
多分、現状での実用精度は 1/100以内って、とこでしょうか〜
(^_^) |
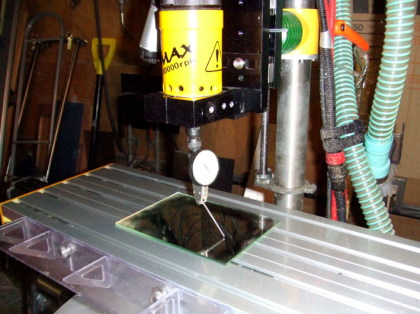 |
一旦、Z軸を外してしまいましたので傾きの調整をします。
テーブルに平面の出ているガラスなどを置き主軸にテスト・インジケーターを銜えさせ前後・左右に走らさせシムをガラスの下に挟み測定面の平行度を出してから手で主軸を360度回してみての調整になります。
ちなみに完成後のZ軸の最大F値は1,400mm/mini 常用値は 1,000程度ですね。
Z軸の掘り込みでは、そんなに速度は必要としないのですがGOOの戻りの速度等を稼がないと複雑な多段彫の場合、総合的な切削時間にかなり影響しちゃいます。 |
 |
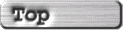 |
 |