|
|
|
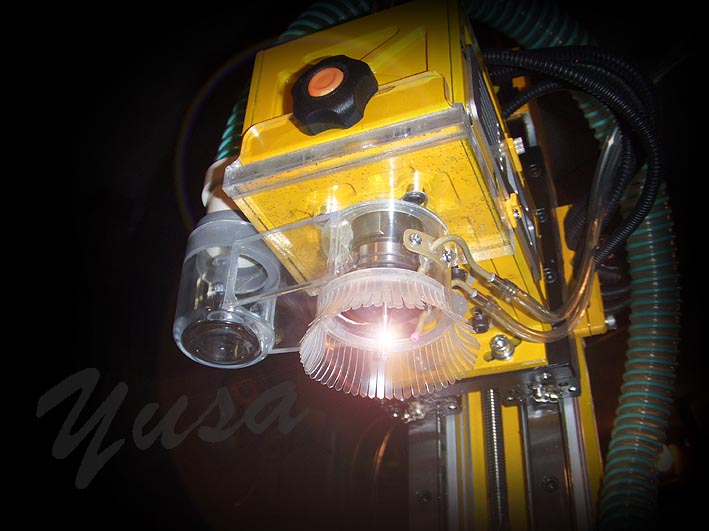 |
自作mini-CNCの主軸のアップ・グレードに伴い、今までの集塵ノズルが使えなくなりましたので新たに作りなおす事にしましたので、製作の過程の一部をご紹介致しますので、もしご参考になれば幸いと存じます。 |
|
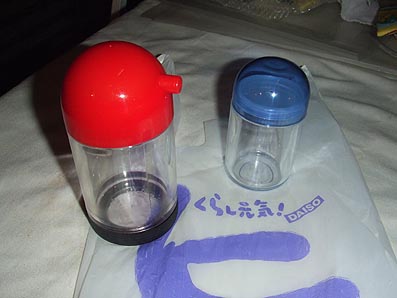 |
【 材 料 】
まずは材料の調達ですがアクリルの丸パイプなどは結構高いので100円均でアクリルの醤油入れと爪楊枝入れを買ってきました。
なかなか肉厚ですし、これは良いゾ !
(^。^)
恐るべし "百均 ! " 恐るべしDAISO !
ここで気をつけなければならない事は使用する材料は全て同じ材質に揃える事です。
以前、今より無知だった頃、透明な樹脂なら、どれでも同じだと思い加工した後に接着しようと思ったら全く接着できませんでした。
多分、塩ビとアクリルの組み合わせだったのか・・・ (^^ゞ
と・言う事で今回はアクリル&ポリカに統一しました。
次にベースになる部分ですが、丁度良い厚さ(12mm程度)の物が手元に無い・・・・・
(ーー;)
よし! 6mm 2枚を接着して使ぉ〜! |
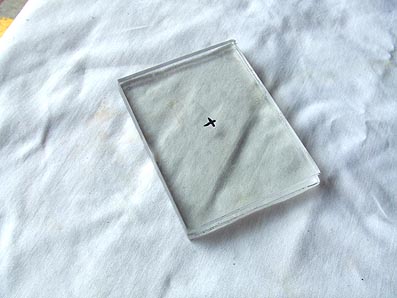 |
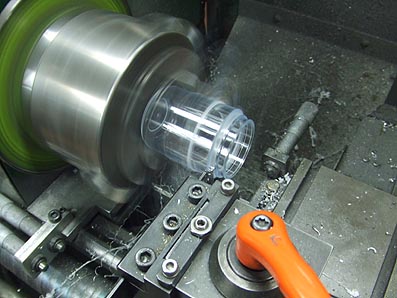 |
【 加 工 】
買ってきたアクリルの入れ物を旋盤に銜え突っ切りで必要長さに切り出そう。
・・極・溶けないように極・低回転で慎重に・・・ |
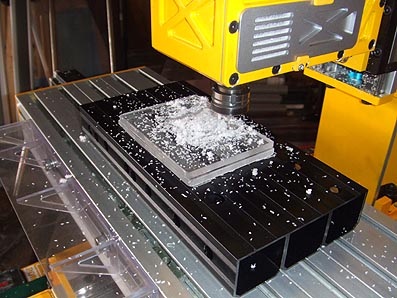 |
ベースになるプレートはCNCで切削 !
集塵が無いと、メチャクチャ散らかってしまいます。
(ーー;)
早く集塵を完成させないと・・・・! |
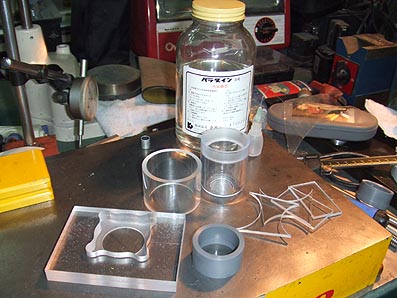 |
【 組 み 立 て 】
部品の加工が一通り終わったので、それでは、いよいよ組み立てに入ります。
ここでは加工した部品をアクリル&ポリカ用の接着剤である"パラダイン"をシリンジ(注射器orスポイト)を使って隙間に少量を注入していく作業だ。
慎重にやらなければ・・・・はみ出してしまうと完成時の美観を損ねてしまう。
適量を"ピュッ"と垂らすと隙間に"スゥ〜"と綺麗に入ってくれます。
この時、下向きで作業をする場合に気をつけなければならない事はスポイトタイプを使い中に空気が一杯入っていると手の温度で中の空気が膨張して必要以上の接着剤を押し出して垂れてしまう事がありますので、出来ればスポイトの中を接着剤で満たして使うか、注入の前に充分に手で一旦スポイトを暖めてから下向きでノズルを接着ポイントに近づけるよう気を使う事です。 |
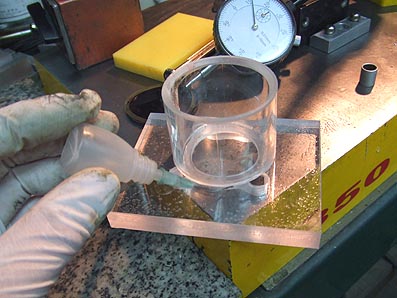 |
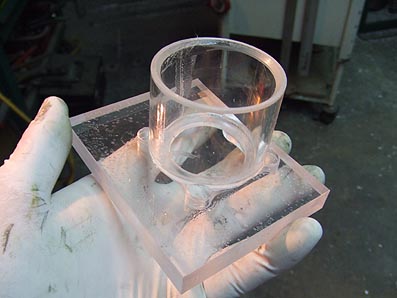 |
大まかに組み立てが完了しました。
パイプ部分とダクト部分の接着が終わったら接続部分の開口をする事を忘れてはいけない。
後で掃除機が窒息してしまいます。
(^^ゞ
私の場合は接着による組み立ての前にフライスでエンドミルを使って所定の寸法に開口しておきました。
フライス以外にリューター等、道具はなんでも構いませんね。 |
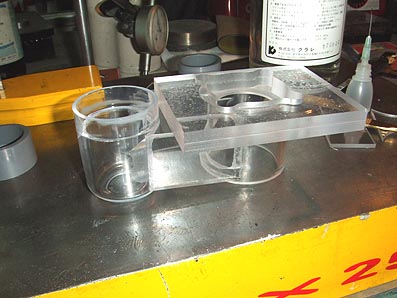 |
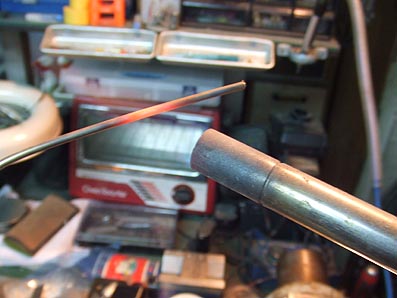 |
集塵のズルにはエァーや切削液のミストを噴出させる兼用のノズルも配置する事にします。
配管はΦ3mm×Φ2mmの真鍮パイプを使う事にしよう。
ただ色々集塵カバーに合わせて曲げ直しをすると硬くなってくるので最初からバーナーで炙って鈍しておこう。
この作業の有無で後の作業が格段に楽になるぞ。 |
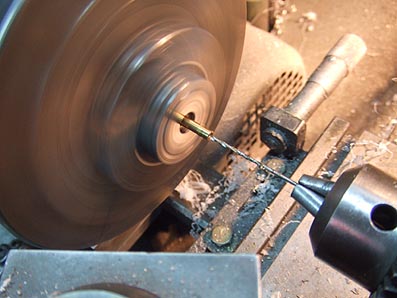 |
さて、エァーブロー用のノズルであるがΦ2.0mmの内径のままでは空気源に3馬力以上のコンプレッサーが無ければ連続使用できない。
ゆえに先端に付ける細径ノズルを別に作る事にしよう。
Φ3.0mmの真鍮棒にΦ1.0mmの穴を開けて作る事にしよう。
左下が完成したノズルである。
これを屈曲させて作ったチューブの先端にハンダ付けで固定する。
噴出エァーが極力、真っ直ぐにエンドミルの切刃に当るようスィープに吹かせる為にノズル内径の直線部分はノズル内径の約5倍は必要なので10mm程の長さに作った。 |
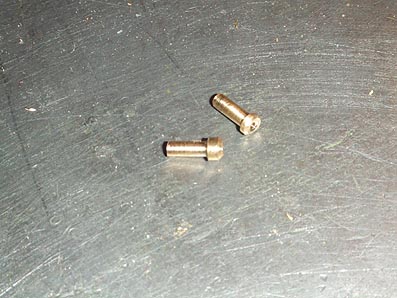 |
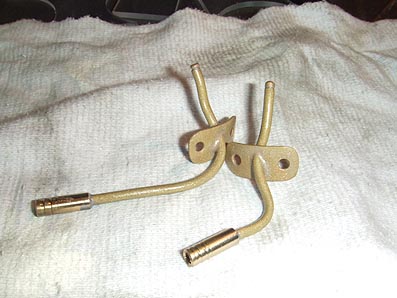 |
完成したエァー・ブロー用のノズルである。
手前側の太径の部分はホースと径を合わせる為の取り付け口である。
集塵カバーへの取り付け用プレートは0.6mmの真鍮板から切り出し"銀蝋付け"で固定しよう。
なぜ銀蝋付けかと言うとノズルの向き等、後から結構パイプを動かす事が予測されるのでハンダ付けではもたないのと他のパーツをハンダ付けする時、この部分が溶けないようにである。
加工後、得意のサンド・ブラストをかけクリア塗装を施した2本のノズルである。 |
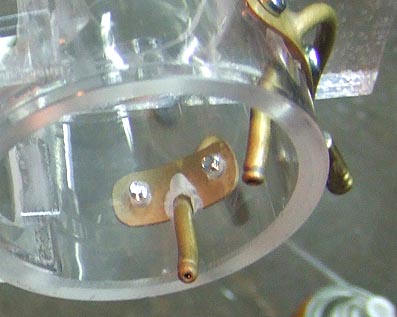 |
実際にM3のビスでノズルを取り付けたところである。
切削した溝の中で走るエンドミルの切刃に確実にエァー・ブローが出来るように90度位相をずらして計2本のノズルを配置する。
場合によっては片方の1本からは切削液をミストにして吹く事も可能だ。
このノズルの役目は基本的に切削屑を吹き飛ばすだけではなく刃物の冷却も兼ねている。 |
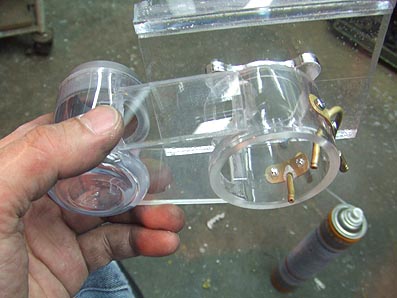 |
いつもの自画自賛であるが・・・
・・・・・機能的であり本当に美しい作りである。
ヽ(^o^)丿
アクリルの切削面には接着剤を塗って透明度を出しておこう。
それにしても2本の真鍮パイプ製エァーブローのズルのカッコ良い事。
まるでスポーツカーのデュアル・マフラーかバイクの集合管のようである。
私の格言『機能を追及すると美が生まれる』・・・・・
・・・・なんちゃって (^^ゞ |
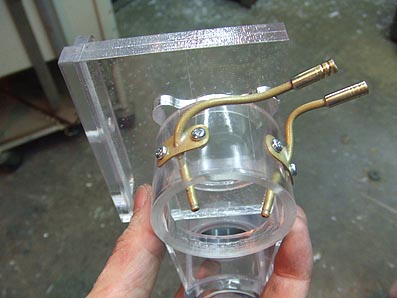 |
どんなに良い形状の集塵ノズルを作っても集塵機(掃除機)の能力には限りが有るし、また主軸はプログラムにより常にZ軸が降下/上昇し切削材料との間隙は一定ではない。
しかし完璧な集塵を求めるのであれば極力、集塵ノズルと切削材料の間隙は少ない方が良い。
この矛盾した関係を改善するのが"スダレ"である。
色々とブラシなどを流用してみたが中々良いものが見つからず行き着いたのが、コレである。
事務用の"クリア・ファイル(塩ビ製)からローランドのカッティングプロッターを使って切り出して作る方法である。
これを両面テープを使ってノズルに固定しよう。
この時の、チョットしたテクニックが有る。
切り出したスダレの毛先部分に当る部分を100円ライターで、サァ〜っと融かして切断面を丸めるのである。
こうする事によりスダレのモチが大きく変わってくる。
この処理をしないと、どうしても使っているうちに切断面から割れてボロボロになってくる。
結構、考えているでしょ〜
だって、かなり苦労したんだモォ〜ん
(^^ゞ |
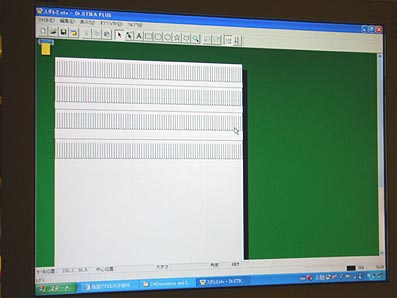 |
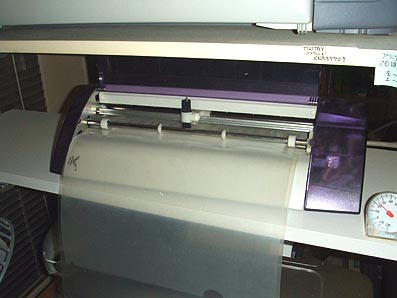 |
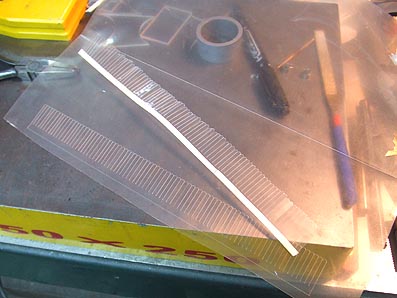 |
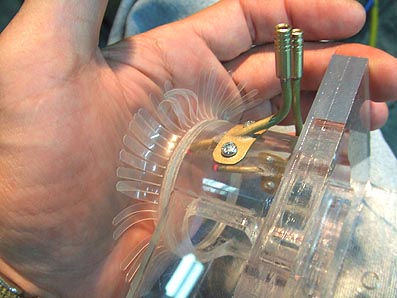 |
次に両面テープで取り付けたスダレを掌で軽くしごいて外開きの癖を付けます。
また・・・これをしないとバキュームONで内側にスダレを吸い込み"タンポポのつぼみ"状態になっちゃいます。 |
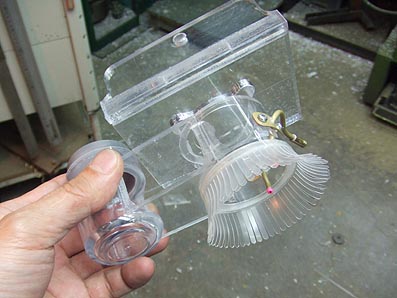 |
・・・・・全、完成です。
それでは主軸に取り付けましょう。
ヽ(^o^)丿 |
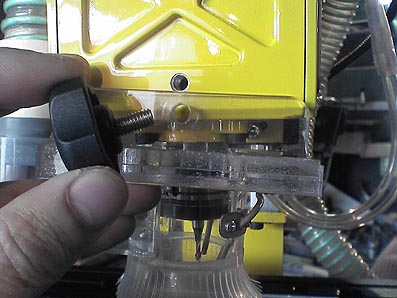 |
取り付けは主軸変速機の正面に加工したM6のタップ穴にグリップ付きボルトで固定します。 |
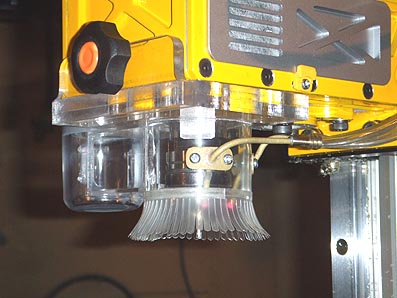 |
うぉ〜っ !
なんか凄そぉ〜 ! |
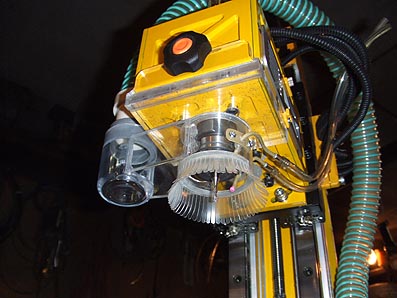 |
・・・って言うか・・・
この方式は旧主軸でも採用して長年の実績のある方法で未だ、これ以上の集塵システムの考案には至っておりません。
m(__)m
もし参考にされて作られる方がいらっしゃいましたら、くれぐれも集塵ノズル部分の有効開口面積をホース内径面積等より絞り流速が早まるように設計する事を推奨します。
サイクロン・ポットを始め、集塵のノウ・ハウは配管内の圧損を抑える事と流速を調整して、いかに吸引を上げるかという事に尽きるかもしれませんね。 |
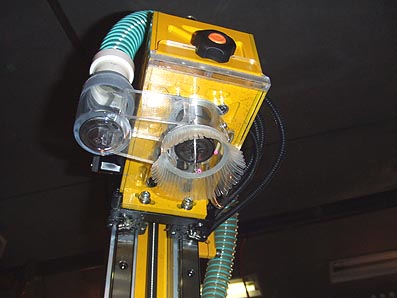 |
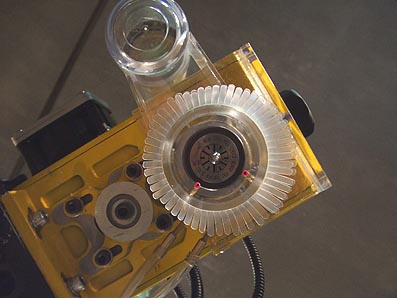 |
一見、大口径のノズルに見えますが実際にスピンドルのコレットの面積を引くとかなり絞り口にして流速を早めて吸引能力を上げている事が解かると思います。
また左の画像ではエァー・ブロー用のノズルの配置も確認できる事と思います。 |
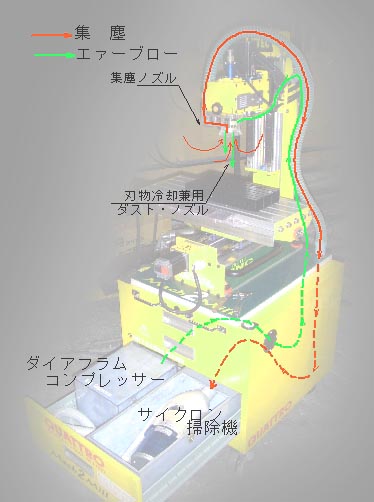 |
左が全体的な集塵、エァ・ブローのフローを説明の為に作ったチョット汚い画像です。
m(__)m
現状は小型のサイクロン掃除機を集塵のユニットに使っていますが集塵容量が少ない為、長時間の加工の場合は何度か塵を取り除かなければなりません。
やはり以前にロック・ヒルさんの掲示板で皆さんが考案されていたように私も本システムの途中にサイクロン式の集塵ポットを取り付ける事も今後視野に入れていかなければならないと思います。 |
|
【 サイクロン・ポッドの製作 】 |
|
|
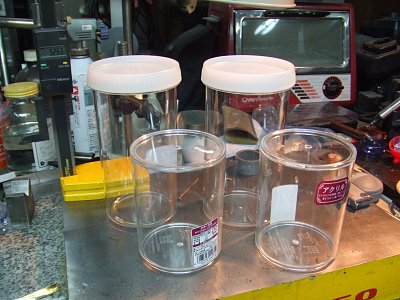 |
【 材 料 】
100均で集めてきたアクリル容器です。
そこそこ使えそうな物がありました。
一応、効果を確認できるように透明の物を選択しました。
|
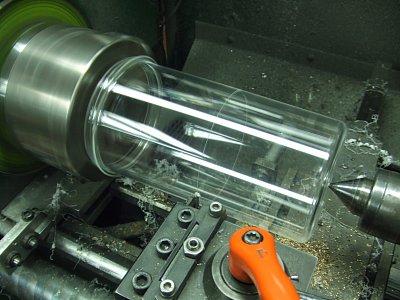 |
【 部材の加工 】
取り合えずサイクロン室と集塵室を上下に分けて作る事にします。
其々、適当な大きさに旋盤を使ってカットしましょう。 |
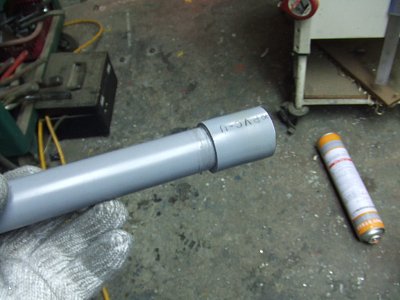 |
CNC本体の集塵システムに取り付ける為に塩ビパイプにソケットを接着します。 |
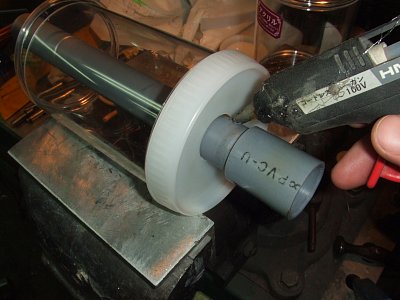 |
次に下側、集塵室になるケースの蓋に穴を開け先ほどの塩ビパイプをホットメルトで接着固定します。
溜まった塵は、この蓋(キャップ)を緩めて取り出す仕組です。 |
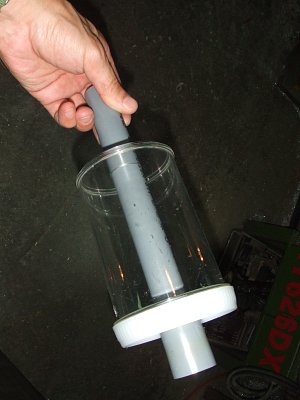 |
完成したサイクロン・ポッドの下側集塵室部分です。 |
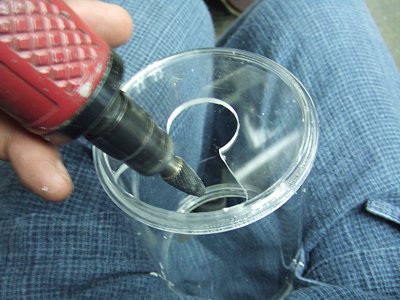 |
上部のサイクロン室と下の集塵室を分離する隔壁を作ります。
回転した塵を下の集塵室に落とす為の開口部をリューターなどであけます。
ここで重要な事は内径ギリギリまで穴を拡大し壁面に段差が出来ないように加工します。 |
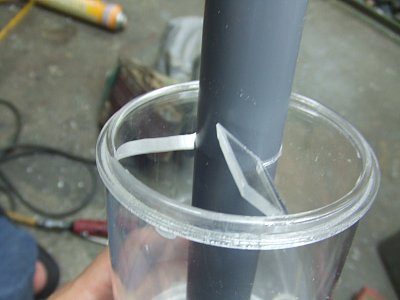 |
下側の集塵室から吸引側のパイプを突き出したところです。
効率良く塵を分離する為にサイクロンの回転方向にあわせて誘い羽を接着します。
また開口部の反対側切り口が非常に厚い材料に見えますが、これは極力切り口に段差をつけないように斜めにカットした部分です。 |
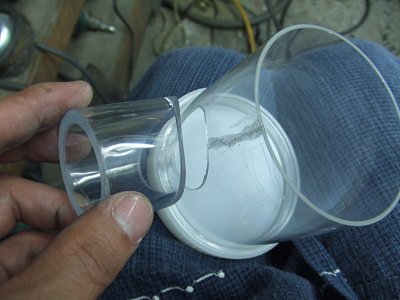 |
いよいよサイクロン・ノズル部分ですが、これも100均で買ってきた楊枝入れをサイクロン本体の胴径に合わせて加工したものを接着するところです。 |
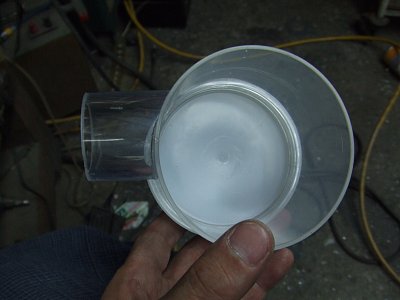 |
完成したサイクロン室です。
もう少しノズル部分を細く絞って、もっと斜めに取り付けるべきだったでしょう。
(^^ゞ
100均で、これ以上適当な物を見つけれませんでした。 |
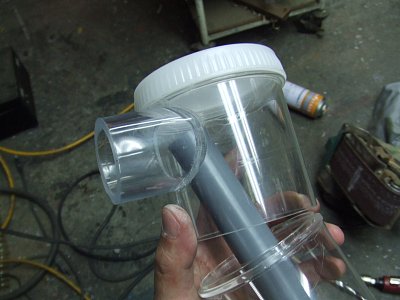 |
いよいよ、組み立てです。
上部サイクロン室と下部の集塵室を接着したら完成です。 |
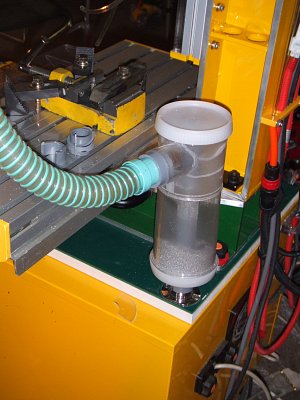 |
【 完 成 】
完成したサイクロン・ポッドです。
はたして、ちゃんと塵を集塵分離してくれますか? |
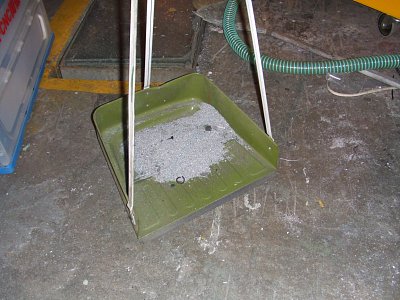 |
取り合えず・・・(私の場合、取り合えず・が・多いです)
実際の集塵に近いようにバンドソーの回りからアルミなどの切削粉を適当に集めてきました。
これで実験しましょう。 |
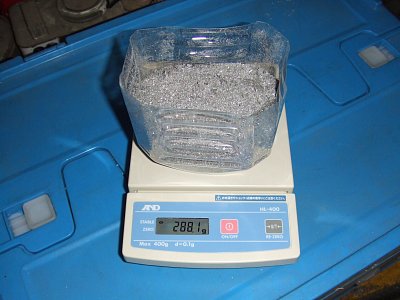 |
まずは集塵させる前に塵の重さを量って起きます。
電子はかりで風袋を差し引いて表示させて・・・
中の塵の重量は 288.1g でした。 |
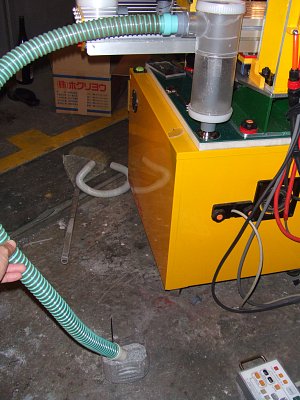 |
いよいよ・・・・(私の場合・・いよいよ・も多いです年をとって来ると掛け声も必要になります)
CNC本体に付けた集塵ノズル(カバー)からホースを取外し先程のテスト用の塵を"一気に"・・・吸わせてはいけませんね。
本番の切削時の吸引を再現するようにホースの先を上手に操り、10分ほどかけて、ゆっ〜くりと少しずつ吸引させてゆきます。
でも、実際の切削で、この量なら本当は1〜2時間位かなぁ〜
まぁ〜でも、こんなんで[良し]と、しましょう。 |
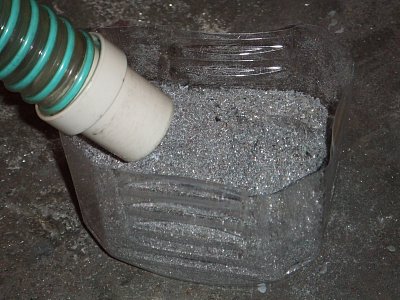 |
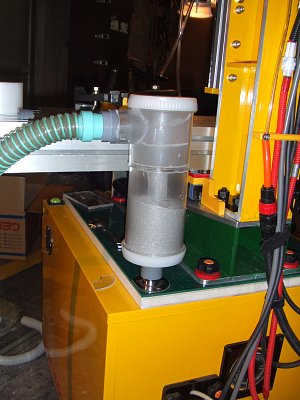 |
おっ、サイクロン室の中でクルクル廻って下の集塵室に見事に落ちていくではありませんかぁ〜
下の集塵室は天上の台風を知らず、いたって静かで平和な感じですねェ〜。
ヽ(^o^)丿
ここまでは、順調で期待通りです。 |
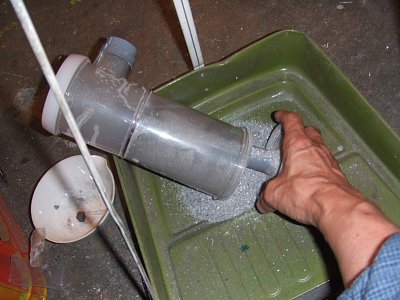 |
さぁ〜てと、全部吸い終わったら、ポットの中の塵の量を測る事にしましょう。
上のサイクロン室には塵が皆無でしたので下側の集塵室の蓋(キャップ)のみを外して中の塵を取り出します。 |
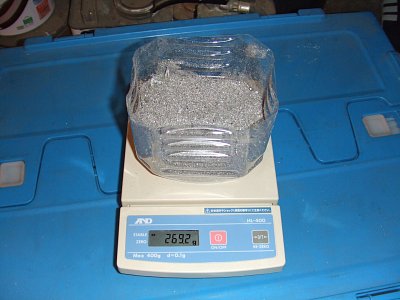 |
では、さてさて・・・・何グラムかな ?
サイクロン・ポッドで回収した重量は 269.2g
つまり 288.1g - 269.2g = 18.9g
288.1g / 269.2g = 93.4%の回収
18.9gが掃除機側に行っちゃいましたが
約90%以上をここで回収できれば成功でしょう。
ヽ(^o^)丿
|
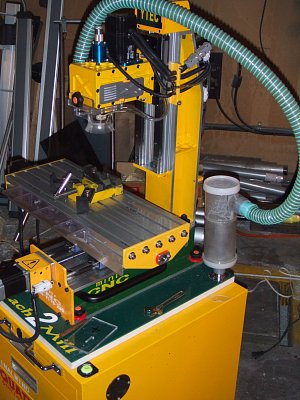 |
【全て完成です】
中が見えたら便利だしカッコイイなぁ〜って思って透明にしたのですが、実のところアルミの塵埃を吸引させたら下側の集塵室は良いのですが上のサイクロン室は、まるでサンド・ブラストをかけた状態で曇りガラスになっちゃいそうです。
今回は図面無しで適当に作っちゃいましたが、サイクロンのノズル部分をもっと改良すれば完璧かもしれませんね。
取り合えず めでたし・めでたし。
(^。^) |
|
|
と・言う事で今回はmini-CNCの集塵用ノズル(カバー?)製作の特集を組み、完結致しました。
もし、皆様の少しでもご参考になれば幸いと存じます。
ご来場誠にありがとうございました。
m(__)m
|
 |
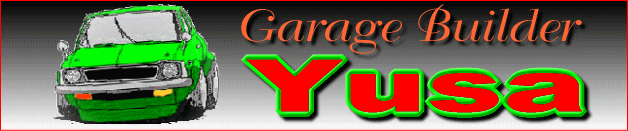 |
゛ |