|
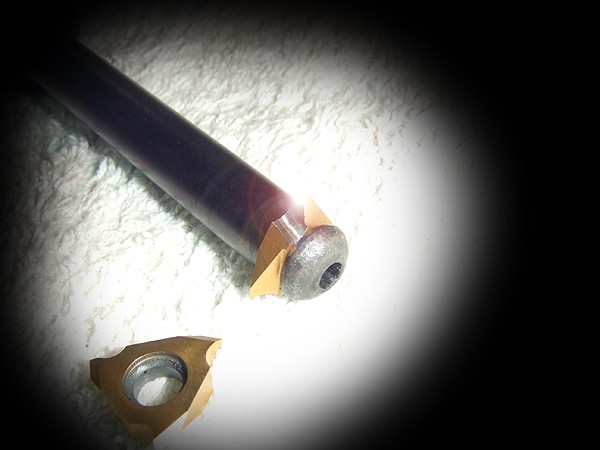 |
【特集】で以前に[Z軸補完によるヘリカル切削]Z軸の補間によるヘリカル運動でネジを切削加工する方法を紹介しておりM6キャップスクリューで刃物を作りましたが、今回はもう少し、それなりの刃物を作ってみましたので、その製作過程をご紹介いたします。 |
 |
** なお[Z軸補完によるヘリカル切削]につきましては下画像を例に別特集で詳しくご紹介しておりますので、そちらをご覧ください。 m(__)m |
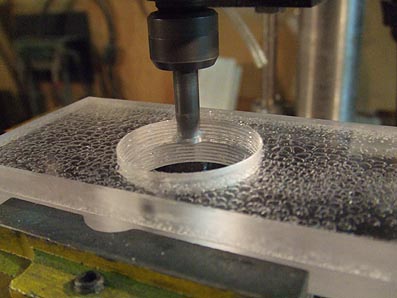 |
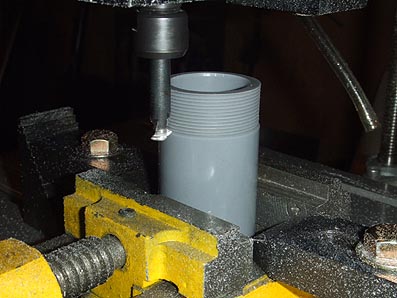 |
|
|
【 一 般 市 販 品 】 |
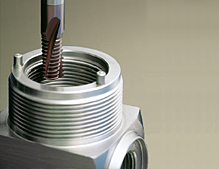 |
汎用機(マシニング等)用としてフライスの三次元軸移動機能を使用する刃物工具として・・
ミルスレッドなどの商品名で同様の物が実際に市販されています。
ただ問題点として一般的な市販品は刃数が多い為に加工するネジのピッチに合わせて刃物を換えなければならないようです。
|
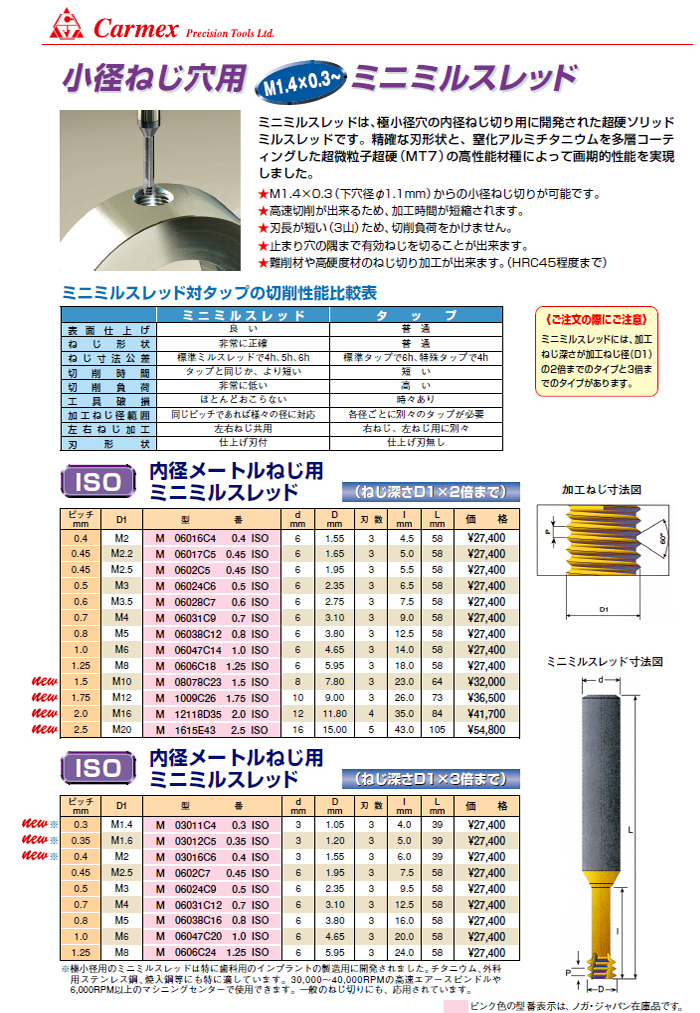 |
|
|
【 材 料 の 準 備 】 |
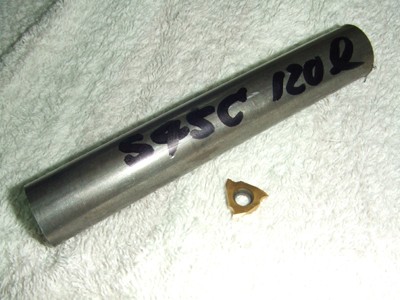 |
【 材 料 】
材料は、どのような物でも構わないのですが、今回のクライアント様(ジェームスさん)の、ご要望でΦ20mmコレットに加えて・且つ深い掘り込みがしたいとの事でしたので・・・・(^^ゞ
材料はS45CのΦ20mm磨棒材でシャンクを作る事にしました。
サイズは銜え口Φ20mm シャンク部はΦ8mm程度で長さ60mm以上って感じデス。
刃先は旋盤の[ネジ切り用チップ]を使ってみましょう。 |
|
【 チ ッ プ の 加 工 】 |
【チップの選定と前置き】
ここで使用するチップは、同形状であればどのような物でも構わないのですが今回使用したチップをご紹介しておきます。
もらい物なので定かではありませんが
・・・・多分・・ [MITSUBISHI] MTTR(L)436000 です。 (^^ゞ
型番の末尾は0〜4までの選択肢があり数値はチップ先端のノーズ径を意味します(0〜0.4mm)
また4桁目のRとLは勝手違いの選択肢となります。
勝手違いはどちらでも良い様に思われがちですがシャンクへの取り付けに影響しますので要注意。
尚、理論的には60度山/谷のミリねじを切る為には大径(40mm〜)であれば、さほど問題にはならないと思いますが、このヘリカル切削において実際にはピッチが粗いほどワークに対し相対的に刃物が斜めに入るとのと同じ結果になりますので切刃後部に、いくら逃げが有っても小径の加工において厳密には切削する谷間部分の角度が60度より大きくなり、またその分だけ山部の角度は狭くなります。
別特集【Z軸補完によるヘリカル切削】の記事の中でも振れていますが、より精密なネジ加工をされる場合において、これらを解消する為には、より小径の刃物を自作するか、もしくは使用するチップの側面を研磨してチップの角度を60度より狭い物にする事が必要です。
この角度の算出については計算で出ますが実際にはカット&トライで試された方がよろしいでしょう。
|
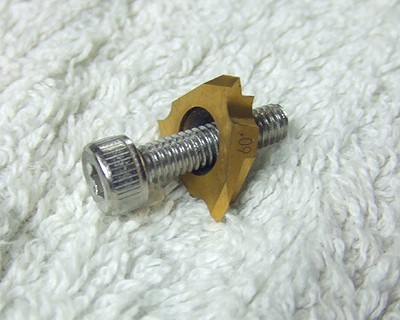 |
【 チ ッ プ の 加 工 】
シャンクに[チップ]を取り付ける方法としてはチップを交換できるようにボルト止めにします。
タップのような重負荷がかかるわけでは有りませんし正回転であればボルトが絞まり方向なので問題は無いでしょう。
・・・・・・じゃ、逆ネジを切る場合は・・・・(^.^)って?
大丈夫です !
ヘリカル切削の場合は主軸は常に正回転させZ軸方向に補完をかける時の回転移動方向(アップカットで切るか、ダウンカットで切るか)で正逆どちらのネジも切削できますので・・・ヽ(^。^)ノ
という事で止めネジを選定したいのですがM4は"緩々"・・・・ (ーー;)
M5は太過ぎて入りません(取りつけ穴径は実測で約Φ4.78mm程度でした)
基本的に"緩々"は論外・・何とかM5で"ピタット"取り付けれるようにしましょう。
(^^ゞ |
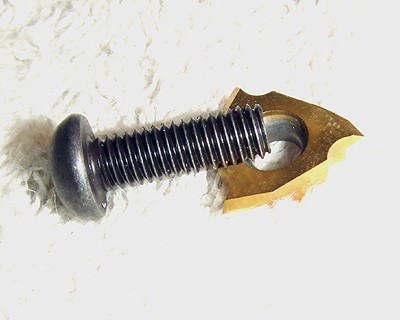 |
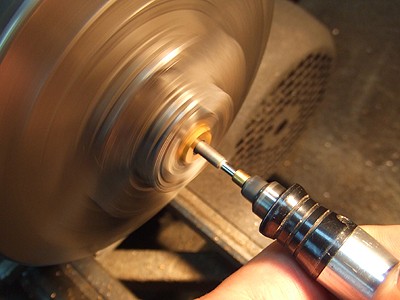 |
【チップの内径加工】
旋盤にチップを銜えさせて回転させて
マイクログラインダー(エァーリューター)に取り付けたダイヤモンド砥石で慎重に穴を拡大してゆきましょう。
焦らずに少しずつやれば超硬チップの穴も[曲がり真っ直ぐ]で綺麗に真円を出した穴拡大は簡単にできちゃいます。
この時、重要な事は穴径を測定器だけに頼らず少し削っては使用するボルトを入れてみる・と言う地道な作業が成功の鍵をにぎります。
当然、ダイヤモンド砥石にはSPECIAL切削液を塗布しての作業です。
|
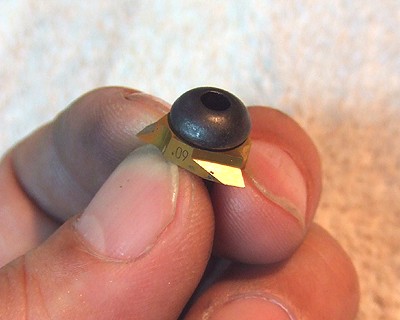 |
おっ〜おぉ〜
ピタッと、いきました。
さすがぁ〜 って自画自賛・・・・は、まだ遠慮しときましょう。
まだ、何が起るかわかりませんから・・・・(^^ゞ
取り付けボルトはM5ボタン頭のクロモリ製キャップスクリューにしました。 |
|
【 シ ャ ン ク の 加 工 】 |
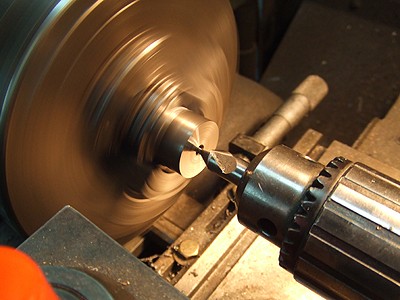 |
【シャンクの加工】
まずはS45C Φ20mm材を所定の長さ寸法で両端の面加工を施し両端面にセンタードリルでセンター穴を開けましょう。
この時重要な事はセンター穴のテーパー面を限りなく綺麗に仕上げる為に必ず切削剤を塗布して作業しましょう。 |
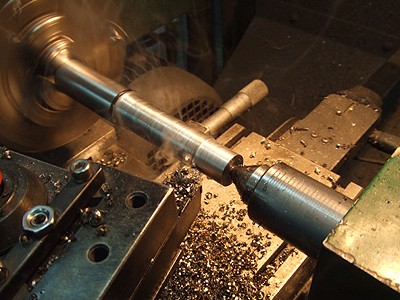 |
次にシャンク部分(細径部)を所定の寸法プラスまで荒取します。
普通の粗物の場合は、当然回転センターで押しますが、寸法精度(芯精度)の厳しい物は超硬チップ付の固定センターにタップリOIL(モリブデン添加)を塗布して押します。
また注意点としてチャック側はあまり深く銜え込まない事です。
私の場合は2mm程度しか銜えていません。 |
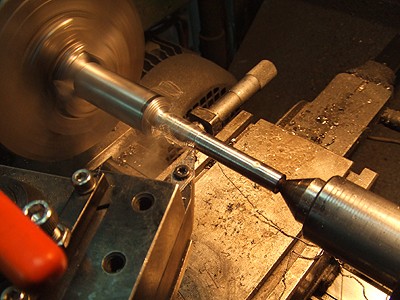 |
次にバイトを換えて仕上げ切削をします。
この時も十分なSPECIAL切削液の塗布を忘れずに行います。
お〜っ ピカピカになってきました。
この部分の外径寸法は芯さえキチッと出ていれば機能的な事を考慮しても径には特に精度に拘る事は不要でしょう。 |
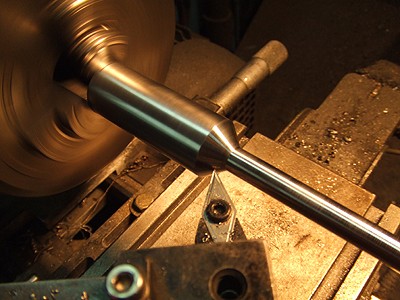 |
段違いのテーパー部分を切削します。
別に何と言った特殊な作業でもありません。
適当な角度に刃物台を傾け斜めに送るだけです。
ただ、ここで重要なポイントは・・・細径側からのテーパーの始まりの根元部分は絶対に切り込まない事です。
出来ればノーズ径の大きなチップを使い極端な括れを作らない方が良いでしょう。
折れるとしたら必ず、この部分で折れます。 |
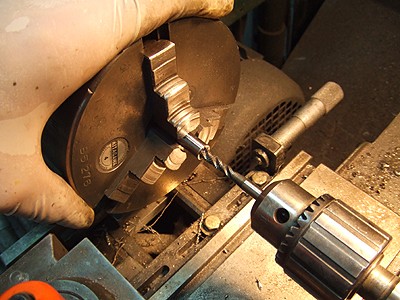 |
次はタップたてです。
先程使ったセンター穴を基準に下穴を開け(私の場合M5はΦ4.1〜4.2mmにしています)ます。
下穴が適当な深さで開いたら次は、いよいよタップたてです。
真っ直ぐにたてる為に芯押し台にセットしたドリルチャックにM5のスパイラルタップを銜えさせて静かに送り食い付いたら、後は手で旋盤のチャックを回してゆきます。
勿論、タップのリードで芯押し台が移動できるように、芯押し台はロックせずフリーにしておきます。
|
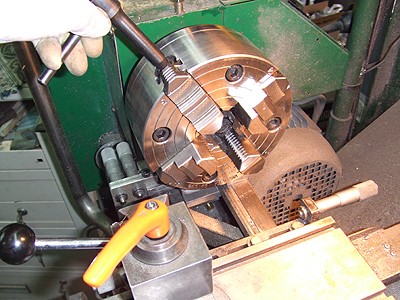 |
次の作業は、ちょっとデリケートな作業なので旋盤のチャックを[4つ爪]に換えて作業します。
別に[3つ爪]でも繊細にセットすれば問題ないのですが一応・・・・教科書とおりに・・・(^^ゞ |
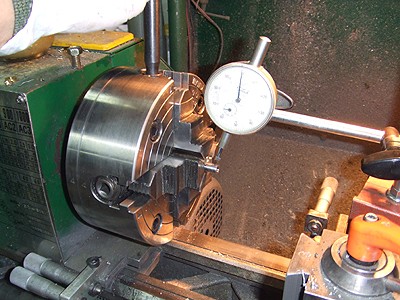 |
4つ爪チャックにワーク(シャンク)を挟み込みダイアルゲージを当てシャンク突端のセンターを出します。 |
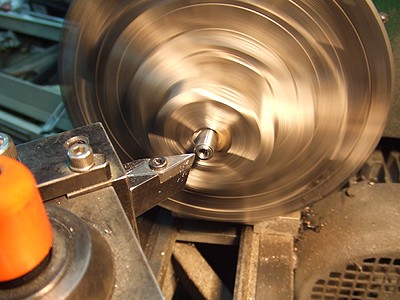 |
いよいよ加工です。
チップを固定する時のセンターを出すのに、いくらチップの内径とボルトの外径がピタッとしていてもボルトの当りだけに頼るのは野蛮ですのでチップ自体に加工されているインローの段付部分に当てる(嵌る)用にシャンク突端も加工しましょう。
ここでチップのセンターが決まりますので手の込んだ芯だしをしていたのです。 |
|
【 シ ャ ン ク の 焼 き 入 れ 】 |
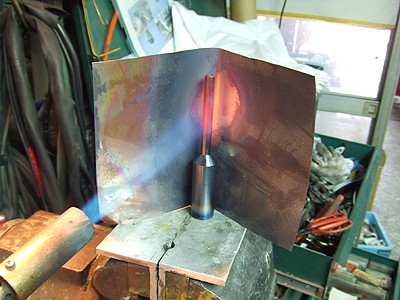 |
この工具は基本的に負荷の軽い工具なのでS45Cの生地そのままでも特に問題は無いはずであるが試しに[焼き]を入れてみよう。
問題は冷水を使った[ズブ焼き]なので、かなり深く焼きが入るが冷水に落とした時に私の腕では・どの位、反(変形)するかわからない。
取りあえずガス・トーチで炙って見ましょう。
どんどん熱が入って行きます。
赤黒い色から、綺麗な赤に変わってゆく・・・・
おおよそ、この時が850℃〜900℃ではないかと思う。
銜え口には極力焼きを入れないようにする。
相手機械のコレットを痛めない為とコレット内で滑りを起こさせない為だ。
息を呑む・・・・冷水に『ジュワ〜』・・・・手ごたえ有りだ。
完全に焼きが入った、但しこのままでは硬すぎて焼き入れによる歪を修正する事も出来ないしシャンク事態の粘りも無く、ただ硬いだけで使用中に共振して使い物にならない。
と・言う事で炉の温度を280℃にセットして1時間程加熱し数時間かけて除熱し焼きを戻す事にした。
俗に言う・・・[焼鈍]である。 |
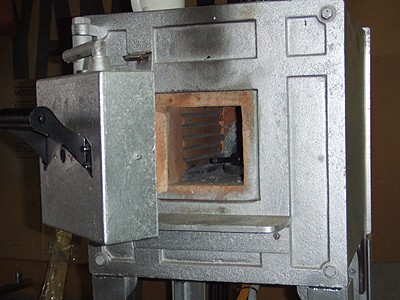 |
|
【 シ ャ ン ク の 振 れ 修 正 】 |
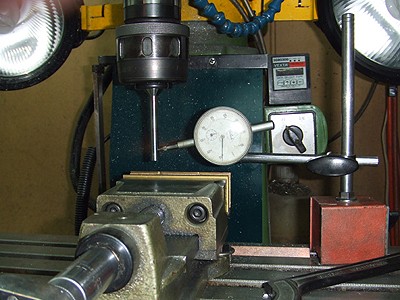 |
【 振 れ 修 正 】
それでは完成したシャンクの[振れ]を修正しよう。
まずは現状の把握である。
作業は実際のフライスのコレットに銜えて行う。
私の機械の主軸(コレット)の振れは定例検査で約3/1000である事はわかっている。
ダイアルゲージを当てて手で主軸を回転させて見る・・・・・と・・・・
うわ〜 (@_@;) 9/100 ・?
(T_T) やはり焼きを入れる時に反らしてしまったようである。
日本刀じゃねェ〜んだから反らして・どぉ〜する
でも実は最初から想定していた事なんですが・・・(^^ゞ
てな事で振れを修正しよう。
まずダイアルを頼りに振れている方向と位置を見つける。
次に最大に振れている位置をコレットにマジックで印を付けよう。
位置が分かったら先端をバイスの淵に当て(真鍮の口金)カウンターを見ながら振れている方向と逆側に押してやる。
振れを計っては押し、計っては押し・・・・・・
これを幾度と無く繰り返し振れ幅を小さくしてゆく。
|
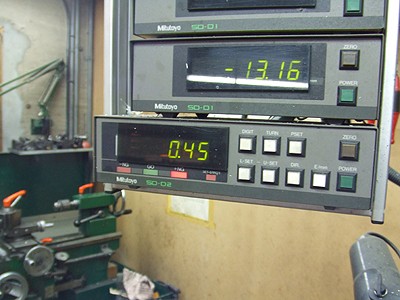 |
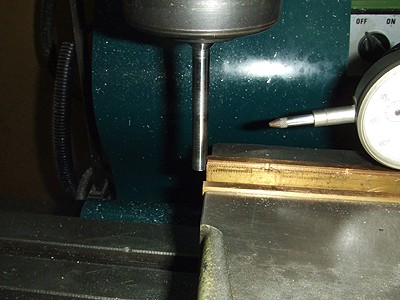 |
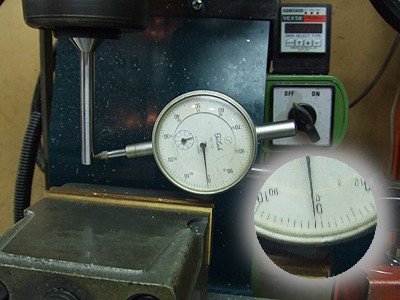 |
よぉ〜し !
振れが 1/100〜2/100と小さくなってきたぞぉ〜
基本的に、この刃は多少振れていても性能的に大きな問題は無いのだが・・・・
プライドと[じっちゃんの名にかけて(金田一少年の事件簿)]・・・・つぅ〜事で・・・
もう、一押し・・・エイ !
・・・・・・(@_@;)・・・・ポキ・・! |
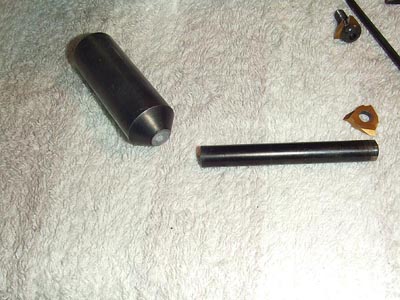 |
・・・・・・・(T_T)
骨折部分の断面を見ると中心まで焼きが入ったままであった・・・・。
焼きは良いとしても[焼鈍]をもっと勉強しなくちゃいけないなぁ〜 反省 |
|
【 気 を 取 り 直 し て 】 |
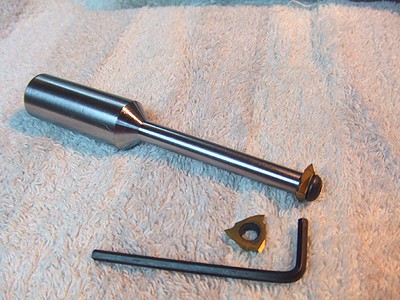 |
ゆ〜っくり(慎重に)作業していたせいもあり
ポキッっいくまでに要した作業時間は[約6時間]である・・・・・。
が・・・・しかし、滅入らず再度、作り直ししよう。
で・一から作り直しました。
m(__)m 焼きを入れるつもりが
逆に焼きを入れられましたので・・
今回は、焼き入れ無しデス・・・・(^^ゞ
でも、さすが2回目、仕上がりは超綺麗 |
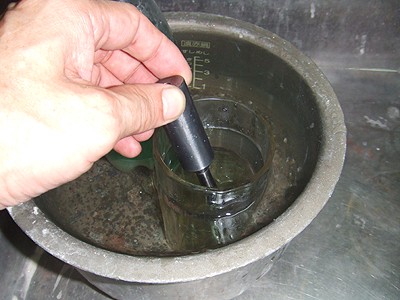 |
せっかくできたのでクライアント様の為に[黒染め]をしましょう。
まずはトイレ洗剤の[サンポール]で脱脂作業 |
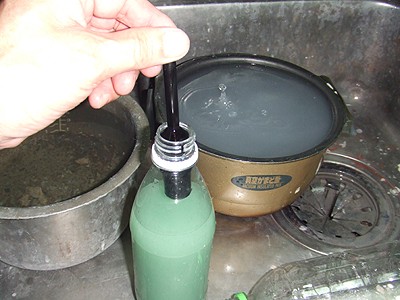 |
次にお得意の[クロゾメリキッド]で黒染め慣行
水洗いは十分に
黒染めのやり方は【特集】の[旋盤用バイトの製作]の中で詳しくご紹介していますので、そちらを参考にしてください。 |
|
【 チ ッ プ の 加 工 】 |
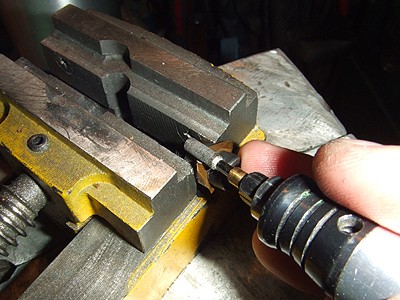 |
【 チ ッ プ の 加 工 】
シャンクが完成しましたので次はチップを加工しましょう。
標準のチップとは使い方が異なりますので[切れ]を良くする為にチップを加工します。
チップをM5のボルト&ナットを使いバイスに固定します。
元々のスクイを基準にスクイの彫りを深くしてゆきます。
いわゆる[スクイを大きくする]って事です。
研削には先程使ったマイクロ・グラインダーに切削液を塗布して削ってゆきます。
くれぐれも元々の切り刃を削り過ぎないように注意が必要です。
|
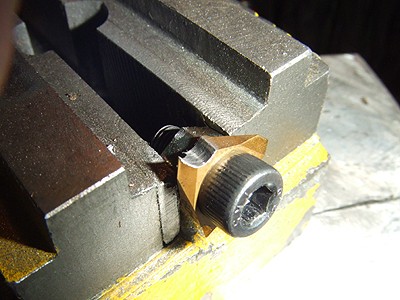 |
|
【 完 成 】 |
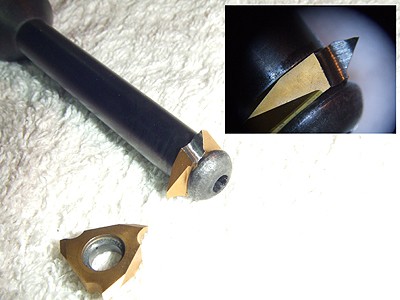 |
【 完 成 】
銜え口の太い(Φ20mm)の部分の黒染めをスコッチブライトで擦って落としましたら
見事に完成です。
先程の"ポキッ"ってのが無ければ自画自賛するところですが今回は自重しておきます。 (ーー;)
・・・・・・途中で大騒ぎして自画自賛しなくて良かったぁ〜
使用したチップはメートルネジの60度を使用しましたのでチップ外径以上であれば全てのメートルネジのオス・メス・正ネジ・逆ネジ・全てのピッチが、これ一本で切削加工が可能なはずです。
そもそも、この3次元軸移動加工(ヘリカル切削)とは歯科医療インプラントねじ製造用に開発されたものでチタン合金のような難切削材の[バリ無し加工]や高硬度材料への加工等に対応した新技術です。
実際に切削加工をしてみると、基本的には主軸の回転数や送り速度の適切な調整により、ねじ切り後の切削面はタップ作業とは違い驚くような表面仕上がりを得る事ができ、感動は抑えられないでしょう。
また、この刃物は旋盤にセットできないワークに対しツール交換する事無く、一本で全てのねじ加工を行える事も最大の魅力です。 |
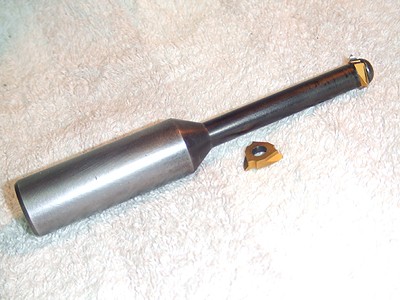 |
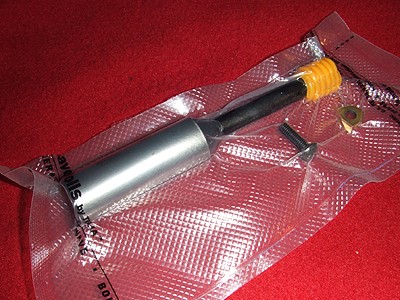 |
【 発 送 】
クライアント様へ発送する為に防錆浸透剤をタップリ吹きかけ刃先には保護カバーを被せ予備部品を沿えて真空パックして荷造り完了。
後は[エクスパック500]に入れてポストイン
クライアント様、シャフトの振れは一応2/100以下まで修正してありますが、前述の方法でお好みの数値まで[修正]して下さいね。
焼きが入っていませんので簡単に修正ができます。
挫折せずに、ここまでの作業時間 [約9時間]
ヽ(^。^)ノ 満足、満足 !
あ〜楽しかったぁ〜 |
|
今回の特集でも、毎度のご期待通り失敗がありましたが、一応・・・完結できました。
今回の特集がmini-CNCファンの方の少しでもご参考になれば幸いと存じます。
m(__)m |
|
|
 |
 |