|
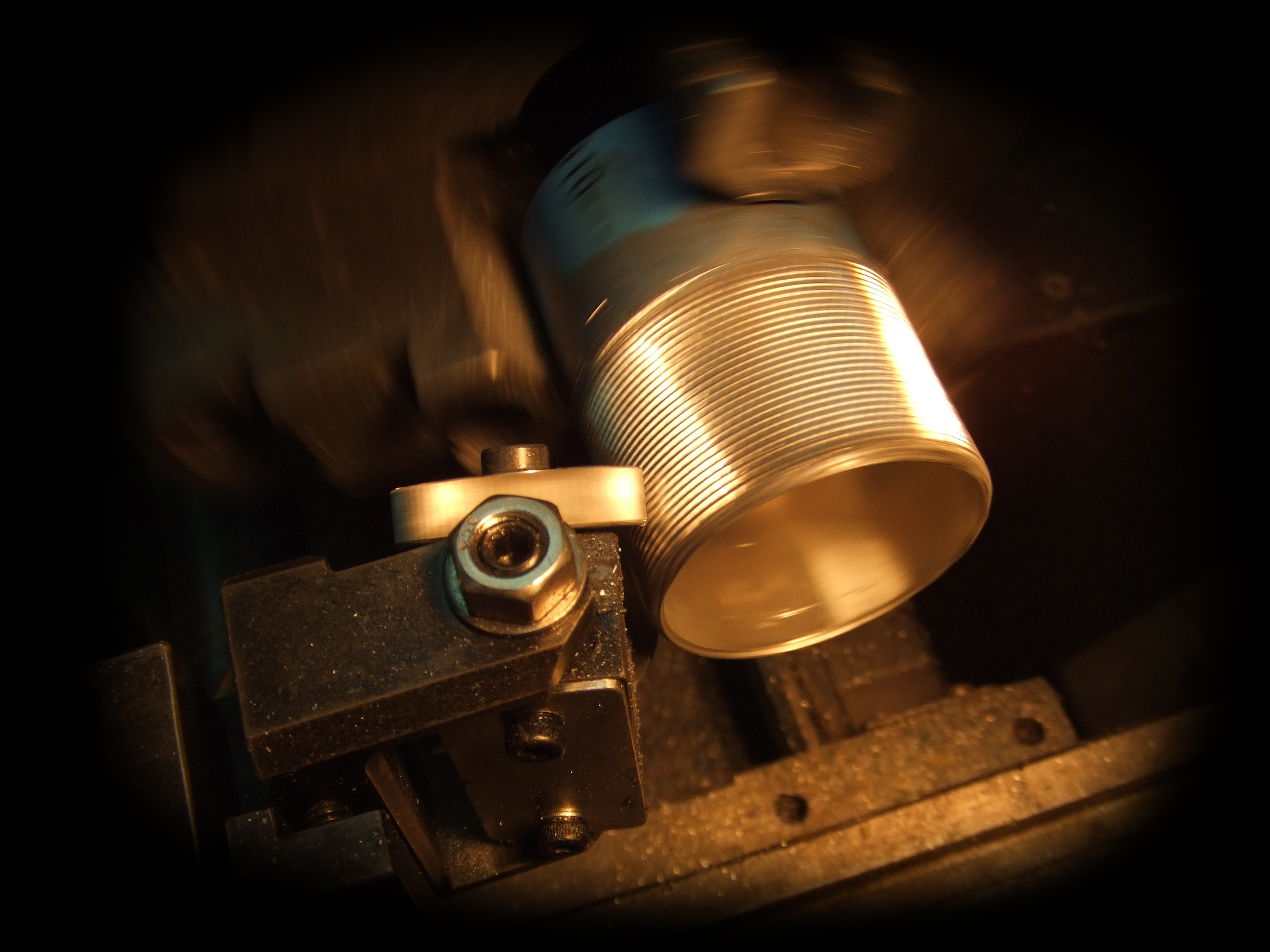 |
皆さんは小型旋盤の加工において既に[ローレット加工]を経験されたか、もしくはこれから試まれようとされると思います。
[ローレット加工]は滑り止め等の機能的な面に加えて装飾的な面もあり、上手く仕上がると非常に満足感が満ちる加工のひとつですね。
しかしながら後述のように趣味の小型旋盤においては非常に機械に負担がかかり厄介な加工のひとつでもあります。
また、プロの世界でも精度と仕上がりを追求すると非常に技術のいる加工であり[機械加工(普通旋盤作業)一級技能検定]の課題にもなっています。
そこで今回は小型旋盤で誰でも簡単に、かつ とても綺麗な[ローレット加工]がソコソコ可能な[切削式のローレット]の作り方をご紹介いたしますので ご参考にしてください。
|
 |
【転造式(塑性加工)ローレットと切削式ローレットの違い】 |
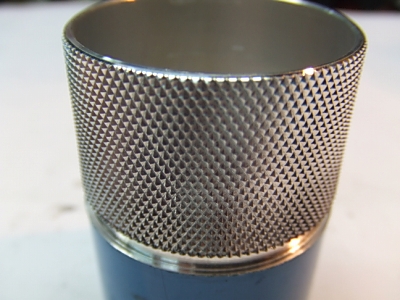 |
【ローレットとは】
「ローレット:roulette」という言葉は、賭博器具のルーレットや裁縫用具のルーレットと同じく回転する器具を意味し、その起源はフランス語にあるようです。英語では「ナーリング:Knurling」といってギザギザの形状のものを意味しますが、ここでは、「ローレット」として統一した名称をつかいます。
一般的に、その加工の大半は、ローレット駒による転造で加工されています。
しかし、旋盤による転造塑性加工で行われる“ローレット掛け”は、一見ラフな加工に見えて、安定して加工出来る条件の範囲が狭い事や、加工条件が厳しくなるほどかなりの熟練が必要になります。
[一般的なローレット駒による転造加工の短所]
@被削材の種類
例えば、ステンレス鋼、樹脂、鋳物、調質材に対しての加工が難しい。
Aピッチの範囲
粗くなればなるほど加工が難しくなり、機械の負荷が極端に大きくなる。
B材料の形状
薄肉パイプ形状や細長いシャフトものなど、剛性的に弱い形状のワークを加工するのは非常に困難である。
C機械への負荷
塑性加工のため機械への負荷が大きく小型旋盤では不可能な場合が多い。
[切削式ローレットの長所]
@被削材の種類が豊富
加工できる材料は樹脂、黄銅、銅、アルミ合金、鉄、ステンレス鋼、チタンなどで、鋳造品、鍛造品、更には調質材(32HRC 程度まで)の加工が可能になります。
Aピッチの範囲
ピッチのサイズによる熟練度を必要としない。
B材料の形状を選ばない
サイズを選ばず薄肉パイプや樹脂へのローレット加工が容易に出来る。
C機械への負荷が少ない 一番の長所は機械やワークへの負荷を最小限に抑えられることです。
また、旋盤本来の旋削で加工を行うため、その負荷が小さく調整に手間がかからない構造になっている。
基本的に押付けタイプに比べて回転数が速い為、加工時間が短い。更には切削面も光沢を帯びていて、山の頂点もシャープに仕上る。
加工時間や段取り時間が短縮できるだけでなく、品質そのものを向上させることができる。
|
いわゆる簡単に言えば、ローレット加工において[転造方式]は力で駒を押付け素材表面をセリ出させて山を造るものであり、かたや[切削方式]は相手の表面に谷間を削り結果非切削部を山とするものです。
つまり小さな機械であれば時間をかけて少しずつ削れば最後には、ちゃんと無理をせずともローレット加工が完成すると言う事です。 |
【 市 販 品 と 価 格 】 |
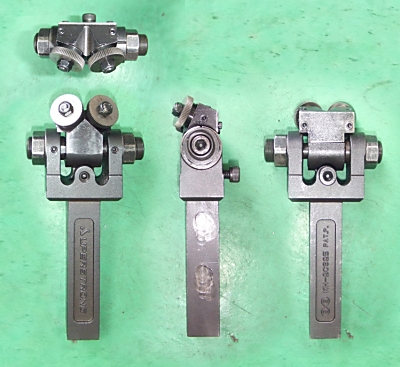 |
【製品価格】
山田マシンツール株式会社や潟Xーパーツールで市販されています。
価格はそれなりに高価で"アヤ目用(駒別売り)で
ホルダーのみ約\70,000程度します
わたし的には、ちょっと手がでませんね (^_^;)
ちなみに"転造ローレット"でしたら\20,000前後ですね。
左画像は当社の工場で使用している潟Xーパーツール製です |
【てな訳で、お金が無いから作っちゃえ】 |
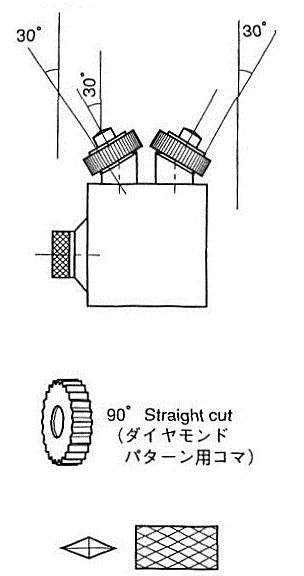 |
基本的にカッタの枚数によりシングルホイールタイプ、ダブルホイールタイプ、トリプルホイールタイプがあるようです。
いずれのタイプもカッタの軸を材料に対して30°ねじって取りつけられる仕組みになっていて、これは削るのに必要なねじれ角をつくるためのようです。
この刃を切れ刃として X 方向へ切りこむと材料に食い付き材料の回転に同調しカッタも食付きながら回転し、それをZ 軸方向に送ることによって、材料が切削される仕組みになっているようです。
これはカッターの枚数に関係なく全て同じ構造になっているようです。
ただし、ローレットのパターンによって、この角度が鈍くなったり鋭くなったりします。
すなわち今回作ろうとしている2枚刃のアヤ目(ダイヤモンドパターン)の場合は30°の切り込みな訳ですから当然、切刃に角度の無い90°の駒を使う事になります。
と・言うか逆に市販品のアヤ目用の90°の駒を使うわけですから必然的に駒の取り付けを30°にすれば良いと言うことになりますね・・・(^_^;)
で・下画像のような設計となるわけです。
一品物の製作ですから基本部分のみ図面化してみます。
あとは端材との現合で何とかなるでしょう。
『重要な事は切刃の取付けが30°と言う事のみです』
|
今回は、私とご同輩の初心者の皆さんが設計しやすいように極力"肝"の部分を記載しますので後述のご紹介内容等を参考にオリジナルを設計してみて下さい。
構造が簡単ですから、そう難しい加工にもならないと思います。
ブロック等の削り出しにはエンドミル等で十分だと思いますし、また気をつけて慎重に加工さえすればリーマ等の加工をしなくても何とかなると思います。
尚、只今仕事の合間を見て図面の手直し行う予定ですので詳細図をご希望の方は当方の[掲示板]の方で一報いただければ、作図が完了次第リリースさせていただきます(メールでのお問い合わせは対応不可ですm(__)m )
|
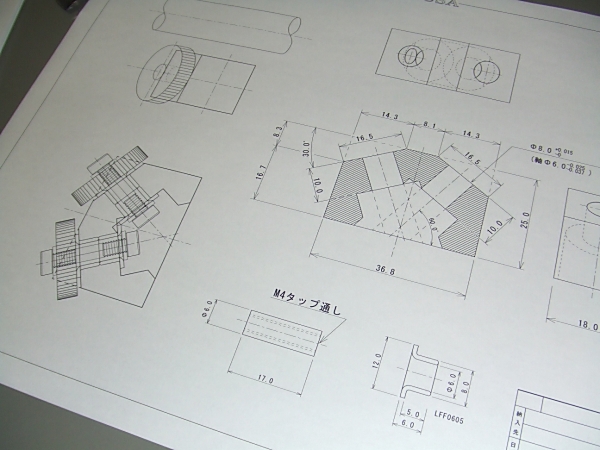 |
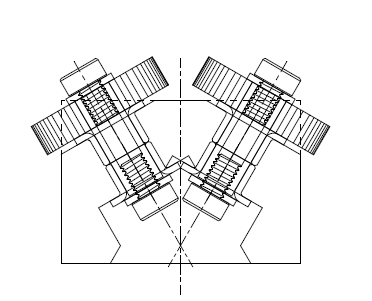 |
【 構 造 】
今回の構造は左図のようにブロックに軸を通して2個の駒を取り付ける構造としました。
今回は軸も回転できるように考えましたが軸を固定して駒だけが回転する構造でも良いかもしれません。
そうするとブロックの底の抜き加工が不要になります。
逆に考え方次第ですが、その方が駒の振れを少なくできるかもしれませんね。
ただし、その場合は駒と軸が回転により焼き付かないように十分に注油する必要があると思います。
この辺を思案の上、設計してみてください。
下図が私が設計した物の抜粋した寸法ですので参考にしてみてください。
|
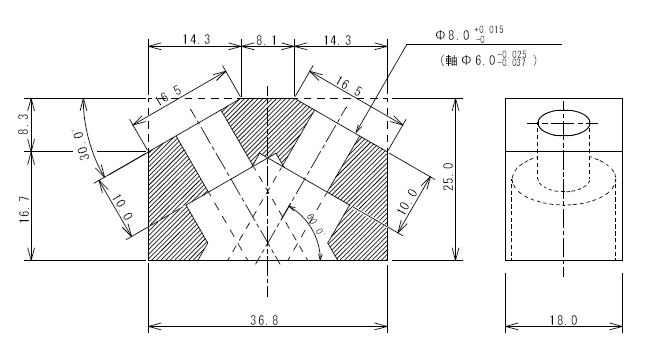 |
【 自 作 ・ 組 立 】 |
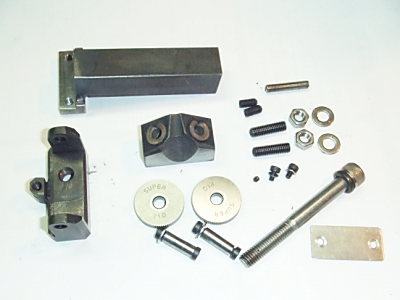 |
【 自 作 開 始 】
前述のスパーツール製を参考に設計し自作しちゃいます。
切ったり・削ったりは図面通りって言う事で、あまり目新しくありませんので今回は割愛しますねっ(^_^;)
そんなんで出来た部品の構成としては、僅かこれだけです。
○ローレットブロック部
○上記ふた
○ホルダー部
○シャンク部
○駒(市販品を購入)
○駒用シャフト
○セットスクリュー及びボルト類(後述参照)
|
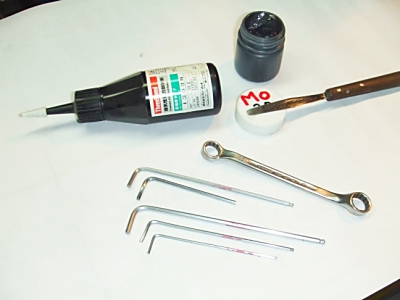 |
【組立必要工具】
組立には何と言って特殊な工具は必要としません。
○六角レンチ数本
○10mmのメガネレンチもしくはスパナなど
○ロックタイト少々
○グリス少々
これだけあればOKです (^。^)
|
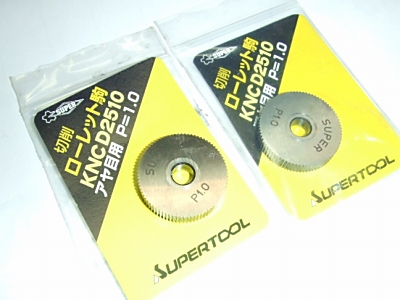 |
【 購 入 品 】
さすがに駒は作れませんので
潟Xーパーツールの消耗部品を購入しました。
ピッチ=1.0 モジュール=0.32
品番KNCD2510 \3,650(定価) ×2個 |
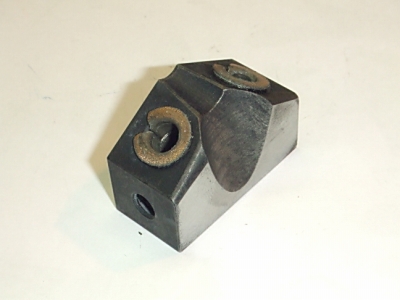 |
【ローレット・ブロック】
このブロックに軸を通してローレット駒を取り付けます。
軸穴にはオイレスのドライブッシュを中・外から挿入しています。
ブッシュの穴は、今回はΦ7.9mmのキリ穴のあとリーマーを通して穴径を調整しました。
が・趣味で使う工具でしたらΦ8.0mmのキリ穴をあけてブッシュにロックタイトを塗布して組み立ててもOKでしょう。
またΦ7.9mmでキリ穴をあけブッシュを圧入し縮まったブッシュの内径をΦ6.0mmのキリを通して調整するのも良いかもしれませんね。
いずれにせよ趣味の世界は"何でも有り"で駄目なら、また作れば良いわけです。
大切なのは、まず やってみる事ですネ (^。^)
それと台形頂部のテーパー形のぬすみはワーク(切削対象物)からの逃げですが実際に使用してみたところ、よほど小径の物を加工しない限り無くてもOKのようです。
左下の画像は全面の画像です。
これを参考に設計されると良いでしょう。
底部の2カ所のネジ穴はM4のタップで蓋を止める為のものです。
また、左右側面にブロックをホルダーに取り付ける為のスタッドボルト(M6セットスクリュー)用にM6タップを立てましょう。
但し、この辺も設計次第では不要かもしれませんね。 |
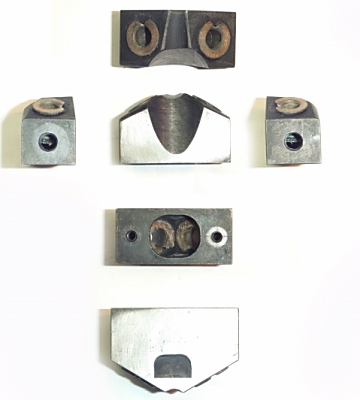 |
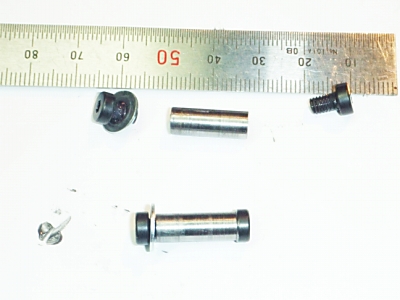 |
【 シ ャ フ ト 】
シャフトはΦ6.0mmの磨きもしくは引抜きの丸棒・・・・
無ければ適当なΦ6.0mm棒で作ります。
両端からもしくは通しでシャフトの中心にM4のタップを立てて駒が抜けないようにM4低頭のキャップスクリューをねじ込めるようにします。
ここで低頭のキャップスクリューを使うのが肝です。
普通のボルトだとブロックの内側で頭が干渉してしまいます。
長さは17mm程度で最初作り組み立ててみて堅くなく/遊び無く丁度良くなるように端面を削って調整します。
駒側には平ワッシャを入れた方が良いようです。 |
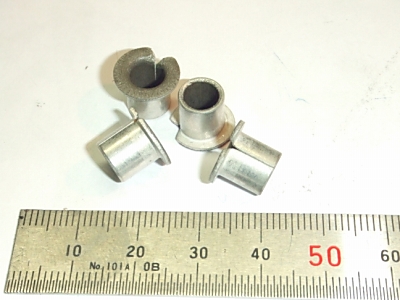 |
【 軸 受 】
切削式は負荷が軽いと言っても、やはり念の為に軸受けにブッシュを入れておきました。これも設計次第では不要ですね。
今回は オイレス工業
オイレス・ドライメットLFブッシュ
型式 LFE0605 ×4個
を使用します。 価格は \100/個 程度だと思います
画像は同系列の物ですが実際に使用するものより長いものです。
私の場合、手元に上記の物が無かったので画像の物を切り詰めて使用しました。 |
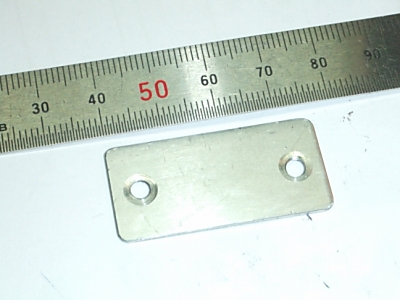 |
【 裏 蓋 】
ブロックの中のグリスが漏れないように適当な板で蓋を作ります。
寸法と取り付け穴は1mmのアルミ板を使いブロックに現合で決めました。
この辺が私のいい加減なところで・・・・ (^_^;)
良い加減・・・かなっ (^。^) |
【 組 立 】 |
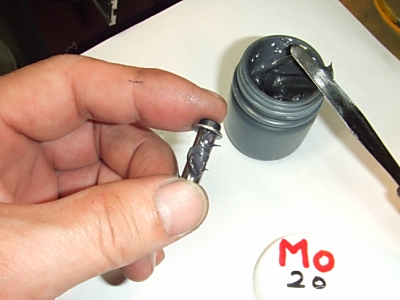 |
【駒の取り付け】
部品も揃ったところで組み立ててゆきます。
まずシャフトの片側にM4低頭のキャップスクリューとワッシャを取り付けシャフトに十分にグリスを塗布します。 |
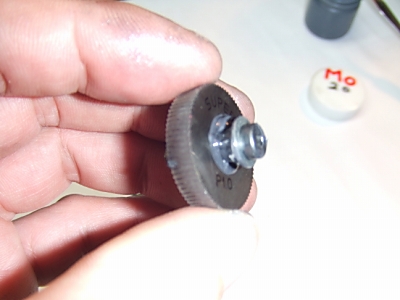 |
駒の裏表は無いと思いますが一応、文字が印刷されている方を表にして組み立てます。
駒の軸穴にもグリスを塗布し、先ほどのシャフトを挿入します。
*駒は端面のピン角で切削してゆきますので磨耗したら裏返して新しいピン角を使えば良いのではないでしょうか。 |
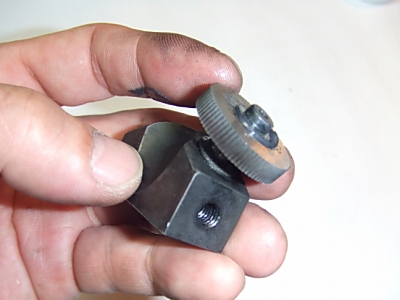 |
駒とピンをブロックのブッシュに挿入します。
もちろんブッシュの内面にもグリスを塗布しておきます。
基本的に、このブッシュはドライで使用できますがオイルやグリスを併用すると著しく性能(耐荷重&高回転)と耐久性がアップするようです。 |
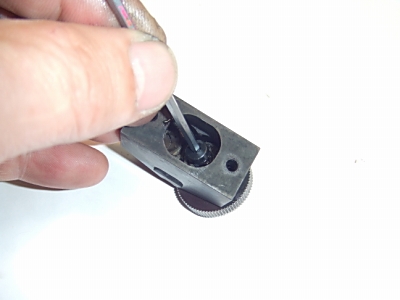 |
次にブロックの底から先ほどと同じく低頭のM4キャップスクリューを使い軸のもう一方にセットします。
こちら側は、単に抜け止めですからワッシャは使用しません。
・・・て言うか、私の設計では ここにワッシャを入れるとキャップスクリューの頭が突き出てしまい低頭の意味が無くなり、もう一方の軸端のキャップスクリューと干渉してしまうのです・・・・(^_^;) |
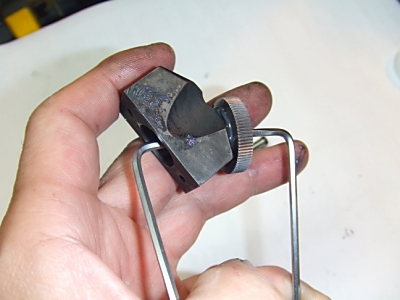 |
軸両端のキャップスクリューを六角レンチを使い確実に締めこみます。
必要であればキャップスクリューにロックタイトを塗布すると良いでしょう。
・・・が、あまり このキャップスクリューに負荷はかかりませんので不要かも ? |
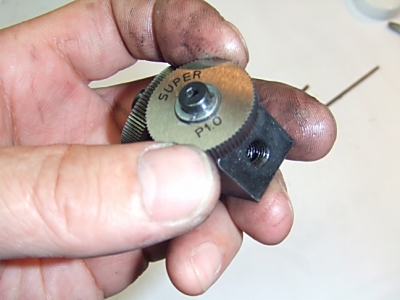 |
この時点で、駒を回して見てガタツキが無く、シックリ回れば良しとします。
"シックリ"って感じは熱したナイフでバターを切る感覚かなっ?
ここで軸方向(スラスト方向に)遊びが多すぎる場合は軸端を削り長さを変える事により調整しましょう。
またガタツキが多い場合も軸を短くしワッシャーの面と駒の端面を利かせガタツキを抑制しましょう。
この方法は邪道ですが趣味の世界は何でも有り・・っちゅ〜事で (^。^) |
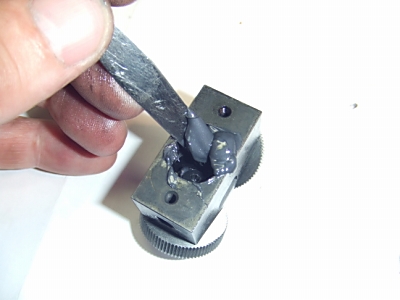 |
2個の駒がブロックに組み上がったらブロックの底からグリスを充填します。
わたし的に、何の意味も有りませんが少しでもグリスが駒側に滲み出てくれる事を期待して入るだけ入れました (^_^;)
*余談ですが高速で回るベアリングやギャーボックスにオイルやグリスを充填する場合は必ず充填量を守る事が必須です。
と・言うのはグリスなどを多く入れ過ぎると回転時に内部で余計な攪拌が行われ抵抗となって発熱の原因となるようです。 |
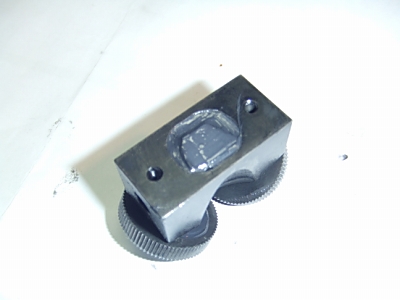 |
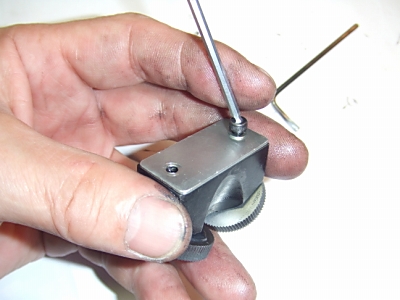 |
グリスの充填が終わればM4キャップスクリュー等々で先ほど作った裏蓋を取り付けます。
これでブロック周りの組立は無事完了です
(^_^)v |
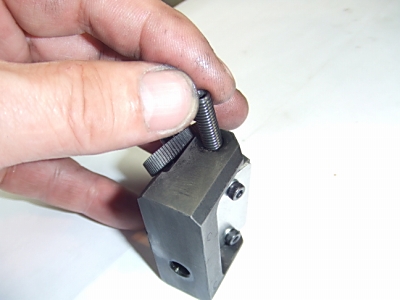 |
【ホルダーへの取り付け】
ブロックの側面に立てたM6のタップ穴を使いホルダーの両端からM6セットスクリューでホルダーにブロックを固定します。 |
 |
ホルダーは左画像を参考に設計されると良いでしょう。
今回、ブロックとホルダーを分けて設計したのは市販品に習い駒のワークに対する接触角度と駒の高さを調節できるようにする為です。
加工はフライスを使い細かな部分は溶接(Tig)による後加工で取り付けです。
が・しかし実際に使ってみると私の場合QTC(クイックツールチェンジ゛)で高さを調整できるし刃物台の振りで角度も変えれますので、もっと単純な方法(ブロックに直接シャンクを取り付ける)でも良かったような気がします。 |
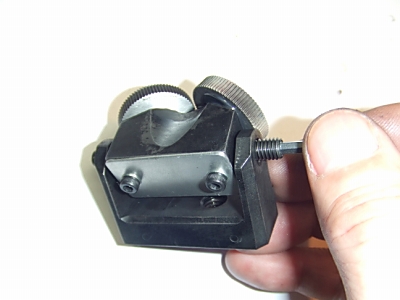 |
まぁ〜取りあえず組立の続きと言う事で、もう一方からもM6セットスクリューをねじ込みます。
この時ロックタイトを使用した方が良いですね。 |
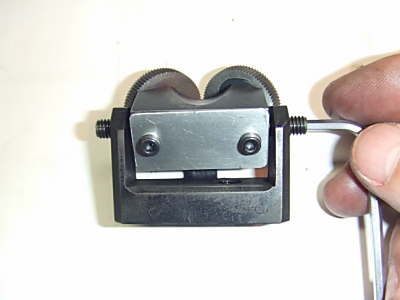 |
ホルダーの両端からセットスクリューを取り付けたところです。
お分かりのように、この時点でブロックはホルダーに固定はされておらずホルダーの中で左右にスライドできます。 |
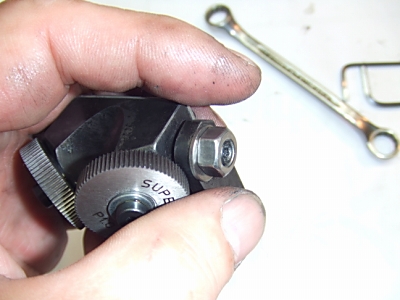 |
両端に突き出たセットスクリューにワッシャーとM6のナットを取り付けます。
もうみなさんお分かりですね。
両端のナットによる引っ張り具合によりブロックの上下位置を調整しようと言う仕組みです。
いわゆる片方を緩め、もう片方を締め込めば、そちらにブロックは寄ると言う事です。
とにもかくにも、取りあえずホルダーのおおよそ中心にブロックがくるようにセットしてナットを確実に締め込んでおきます。 |
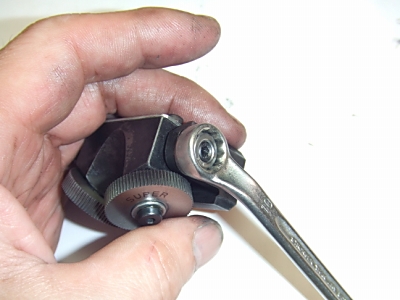 |
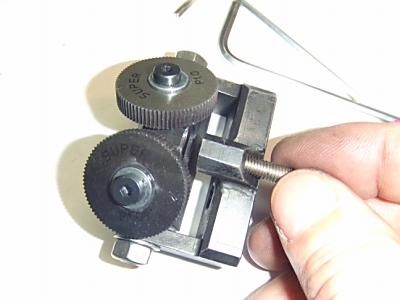 |
これはホルダー側からM5のセットスクリューによりブロックを押し駒のワークに対する接触角度を調整する機構です。
ホルダーの側面に□10mm程度の物をTig溶接し中心にタップを立てて作りました。
・・・・が・この機構も刃物台を振れば無くて良いかも (^_^;) |
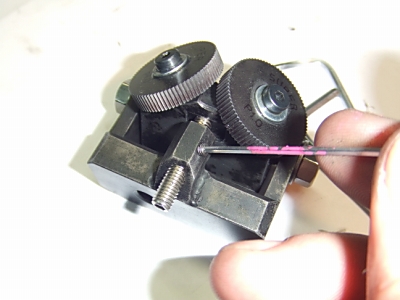 |
上述の押しボルト(M5セットスクリュー)の緩み止めとしてM3のセットスクリュで止めれるようにします。
|
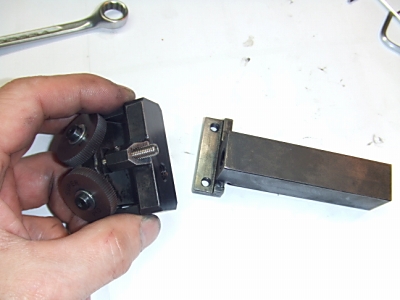 |
【シャンクの取り付け】
いよいよ完成間近です。
シャンクを取り付けましょう。
今回シャンクはガレージの片隅に転がっていた□20mmの角棒を使いました。
このサイズは、皆さんの刃物台などのサイズに合わせ適当な物を選択すれば良いと思います。
また、ホルダー側のM8取り付け用タップ加工位置は、各々の刃物台の高さを考慮して上下にオフセットすると良いでしょう。
|
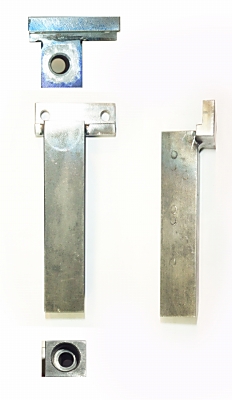 |
シャンクの取り付けはシャンク後部よりシャンクの中を貫通するM8のキャップスクリューによるボルト締めです。
形状は左画像を参考にしていただければ良いでしょう。
構造は、いたってシンプルで□20mmの角棒の中心にΦ8.2mmのドリルで穴をあけ長めのキャップスクリューで締めるだけです。
端部にTig溶接で取り付けてあるプレートは、このプレートにセットスクリューをねじ込みホルダーを押す事によりホルダーを回転させ結果ブロック回転させられ2個の駒の中心線を水平に調整しようと言うたくらみです。
いわゆるホルダーとのジョイント部であるシャンクのボルト穴の上下に押しボルトを配置し(今回均等にはできませんでしたが)、その押し加減で角度を調整すると言う事です。
左画像の上を見ていただくとお分かりになると思いますが、ホルダーと結合するこの部分は少し丁寧に仕上げた方が良いですね。
この面がシャンクの長手方向に対して直角が出ていないとホルダー(いわゆる駒)が捩れて付いてしまいますね。
その為にも、この角度を調整できる機構は必要です。
また同じく結合される接触面については手仕上げにより穴中心方向へ僅かなスリ鉢状にしてボルトを締め込んだ時に□20mmの角棒の端面の外周部が強く当たるようにしておいた方が結合が強く無難でしょう。
|
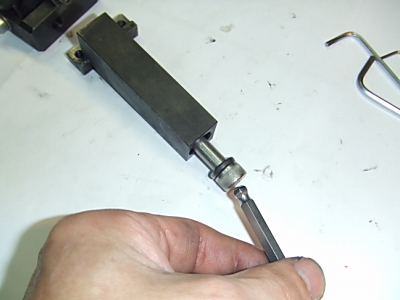 |
と・言う事でシャンクの後部よりM8キャップスクリューを通して組み立てます。 |
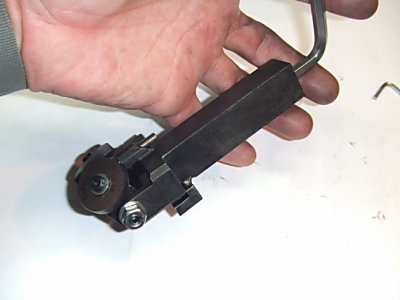 |
取りあえず、おおむね真直ぐな位置にシャンクをセットし六角レンチで仮締めをしましょう。 |
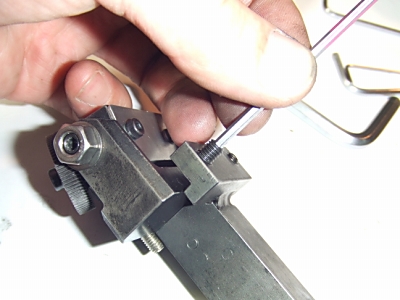 |
上述した2本の取付け角度調整用のM5セットスクリューをねじ込みおおよその調整をしましょう。
取りあえず今回は同じ隙間になるようにしておきます。 |
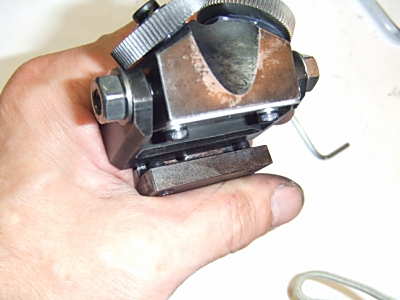 |
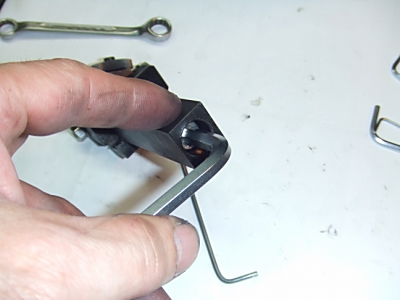 |
最後にシャンク後部より六角レンチを使いシッカリ締めこみましょう。 |
【 組 立 完 成 】 |
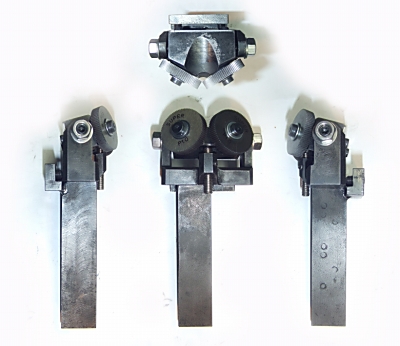 |
左が組立が完了した画像です。
多分もう少しシンプルな構造でも問題は無いと思うのは私だけでしょうか ?
とにもかくにも 完成 !
ばんざぁ〜い
(^o^)/ |
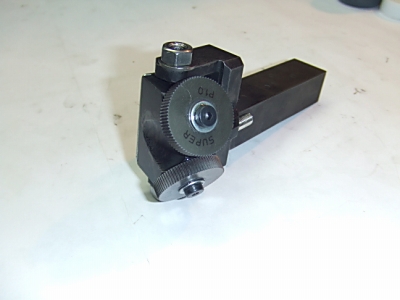 |
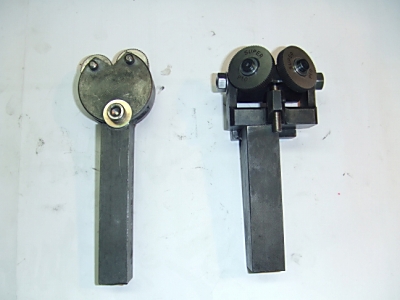 |
ちなみに左側が[転造式(塑性加工)ローレット]で右が今回製作した[切削式ローレット]です。
見た目の大きな特徴の違いは
転造式の駒はホルダーに真直ぐについており駒自体には斜めに溝が入っておりアヤ目が切れる事が直感でわかります。
それに対して切削式の駒は水平な(駒に対しては直角)溝であるが駒が斜めについている。
まぁ〜これは冒頭に記述しましたので、もう説明は不要ですが一目で分かるほど外観が違うと言う事ですね (^_^;)
|
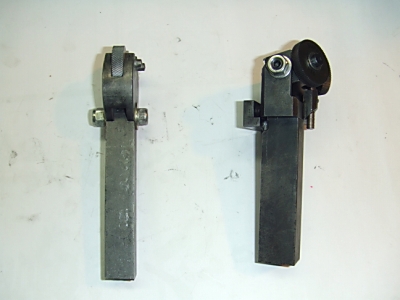 |
【 実 際 の 加 工 】 |
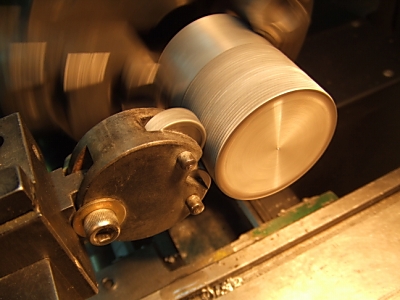 |
[転造式(塑性加工)ローレット]
まずは加工手順と加工結果を見る為に[転造式]で加工して見ましょう。
材料は#6,000のΦ45mmのアルミの丸棒を使います。
旋盤にワークをセットしたら次にローレットを刃物台に取り付けます。
このホルダーは上下に首が振れますので高さは2個の駒の中心がおおよそワークの中心(主軸中心)にくるように合わせます。
また左右の角度は駒が切り込んで入りやすいように時計で言えば2〜3分の位置程度に右に振ってセットしてみました。
極力低い100〜200rpm程度で主軸を回転させワーク左端から徐々にローレットの駒を接触させてゆきます。
ワークと駒が同期して転造が始まりましたら少し強くローレットを押付け左に送ってゆきます。
この時タップリと切削油を与えます。
ワークの表面がローレットの駒の形状に合って変形(塑性変形)してくると負荷が軽くなってきますので、更に強く押し当てて左右にローレットを移動させます。
駒の溝が詰まるようでしたらエァーダスターを使い吹き飛ばします。
常に切削油を与えます。
なんだか機械(旋盤)が、可哀相ですが辛抱して、この作業を5回・10回と繰り返します。
途中で旋盤を止めてみてローレットの目を確認し良ければ終了です。 |
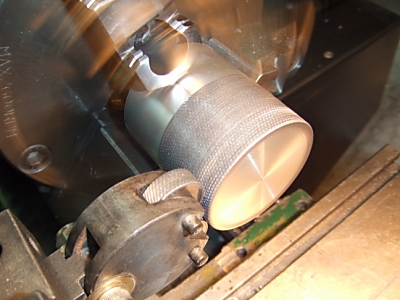 |
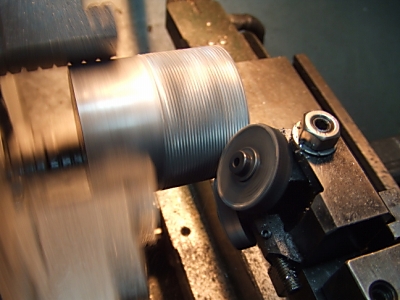 |
[切削式ローレット]
ワークのセットは[転造式]となんら変わりませんがローレットの高さ調整は実際にワークを回転させローレット僅かにを当ててみて2個の駒が同時に接触し同時に回り始める位置に調整します。
左右の角度は転造式と同じく時計で言えば2〜3分の位置程度に右に振ってセットしてみますが、この角度は通常の切削バイトの"逃げ"と同じだと考えた方が合理的かもしれません。
ワークの回転は、やや控えめですが500rpm程度でやってみます。
ワークの回転につられてローレットの駒の回転が始まりましたら切削油を与えローレットを押付け右から左に送ります。
結構強く押付けても旋盤は重たがらず細かな三角の切粉が出てきます。
この時ローレットの駒の目詰まりに注意し適度にエァーダスターで目詰まりを吹き飛ばします。
さすがに私の小型旋盤では一発では行きませんのでワーク表面の目が希望の高さになるまで左右に4〜5回ほど往復させます。
本来の汎用旋盤でしたら一発でいけるのかもしれませんね。
希望の目になったら終了です。
今回は高さと首の左右の振りだけを僅かに調整したのみですが色々トライして条件を出せば、まだまだ良い仕上がりが可能なようです。
何分にも機械(旋盤)への負担(負荷)が非常に軽いようです。
普通のバイトによる切削と大差ありませんね。 (^_^) |
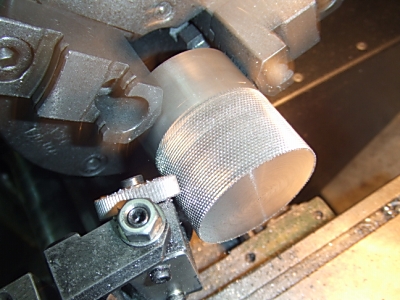 |
【 切 削 結 果 】 |
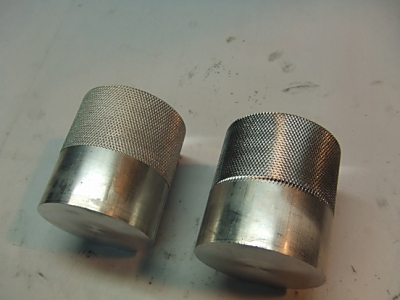 |
左が[転造式]で右が[切削式]の加工結果です |
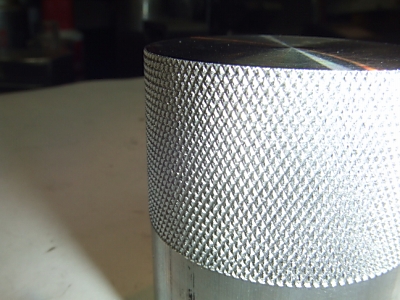 |
上が[転造式]下が[切削式]ですが、明らかに表面の光沢が違うのと切り終り部に特徴が見られます。
やはり[切削式]の方がローレットの山の頂点がシャープなような気がしますし山肌が比べ物にならないくらい綺麗です。
但し何分にも当方、近視の老眼なものでよく見えません。
(^_^;)
|
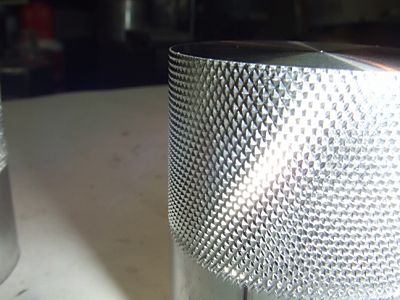 |
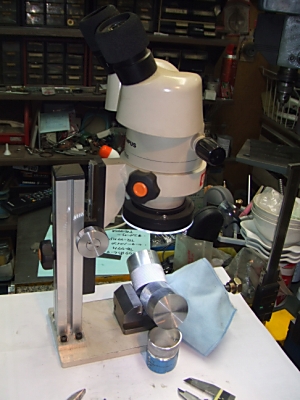 |
てな訳で実体顕微鏡で加工表面を見てみましょう !
左下画像中の左側が[転造式]で右が[切削式]によるものです。
明らかに、その加工方法による違いが分かります。
左側の[転造式]では周りからせり上がって山が形成されているのに対し右の[切削式]では谷を削って形になっています。
また[切削式]の山の斜面に僅かな切削痕が見受けられるのは刃物(ローレット駒の端面のピン角)の切削条件によるものか若しくは数回に分けて段階的に切削した事が理由かもしれませんね。
主軸の回転数を含め、もう少し切削条件を改善すると共に一発で切れれば、まだまだ光沢のある仕上がりになるかもしれません。 |
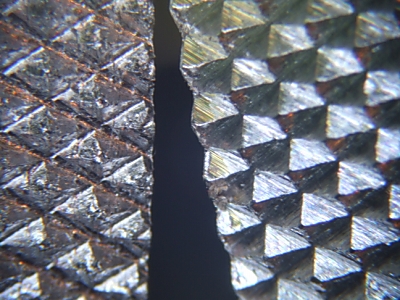 |
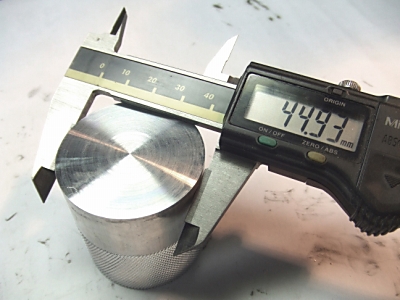 |
【仕上がり寸法】
加工前のワーク寸法は、おおよそΦ45mm程です。 |
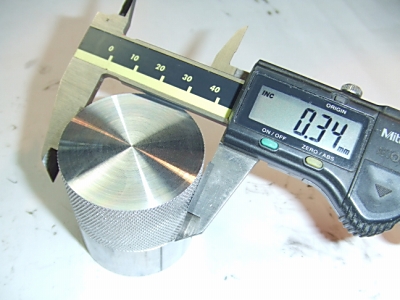 |
[転造式]はローレットの駒により塑性変形されて山が作られますので当然の如く、元の寸法より直径が大きくなっています。 |
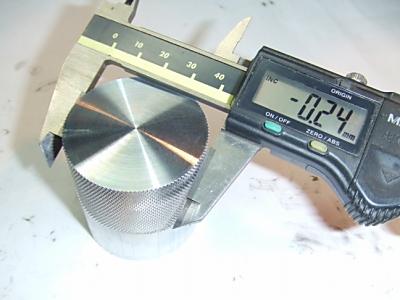 |
逆に[切削式]は字の如く切削により形成されますので元の寸法より小さくなっています。 |
【切削式ローレットの真骨頂である薄物加工】 |
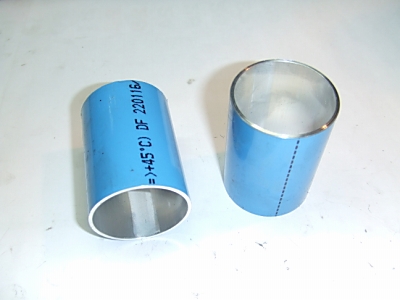 |
切削式ローレットの真骨頂である薄物パイプへの加工をやってみましょう。
材料は、これもガレージの片隅に転がっていたΦ40mm程のアルミパイプでやってみます。
表面に塗装がされていますが材質は#5,000相当くらいのアルミのようです。
ここで問題になるのは厚さです。
測ってみたところ 1.5mm程の厚さでした。
この程度の厚さしか無ければ[転造式]では、ほぼ不可能ですね。(私の腕では、ですが・・・(^_^;) )
|
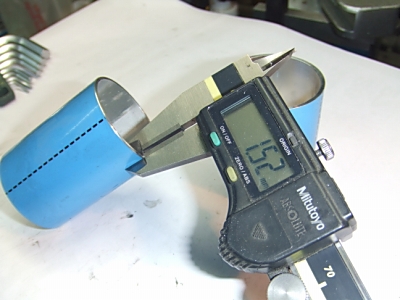 |
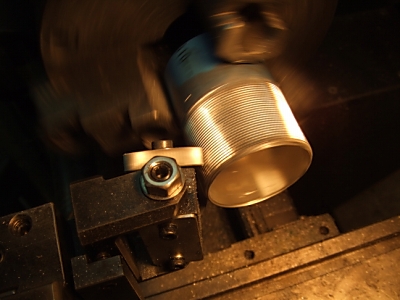 |
先ほどの実棒での加工と同じ条件、同じ要領で行います。
先ほどの材質より若干切削性は良いかもしれません。
数回で軽く加工が終了しました。 |
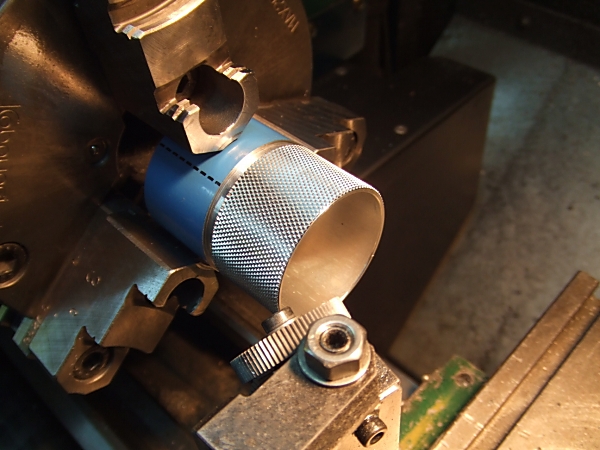 |
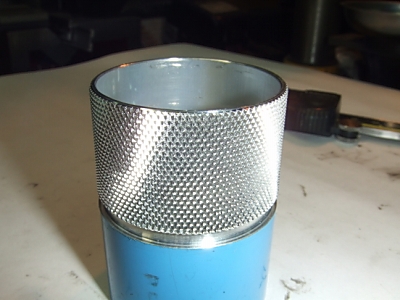 |
我ながら腕が上がったかなって思うぐらいの仕上がりです。
表面の光沢も良く満足行く仕上がりです。
ただ余談ですが[ローレット加工]において、どうして一周して目が合うのか疑問です。
駒それぞれにピッチやモジュールも決まっているのに何故目が一周してズレて行かないのか?
ただローレットの掛け初めは目がダブっている事もありますが加工して行くと次第に目が揃ってきます・・・・(@_@;) ???
これは、私の推測ですが基本的には加工するワークの外周長はローレット駒のピッチで割り切れる値で無ければならないと・・言うか、そうであれば綺麗に加工できるのではと思います。
では、どうして そうでは無い外周長の物でも目が揃うのかと言うと切削であり、転造であれ加工してゆくと最初に付いた目に習って周回を重ねる度に深い目、深い目へと刃先がリードされ結果的に駒のピッチが要求する外形寸法に変化するのではないかと思います。
今回テストしたパイプも加工後には直径が約0.15mm程小さくなっていました。
切削だから当たり前だろうと・言ってしまえば、それまでですが・・・
理論的に谷を削って山を作る訳ですから元の外形と同じ直径を残しても同じ山は作れるはず・・・
と・考えると、きっと この少なくなった直径の時にローレットの駒が要求する直径と一致して目が揃うのではないかと思います。
何分にも私は理論も分からず直感で進む方ですから(^_^;)あくまでも、何の根拠も無く そうじゃないのかなぁ〜って事ですから皆さん信じ込まないようにネっ (^_^;)
でも、とにもかくにも、こんな薄肉のパイプにも簡単にローレット加工ができました。
さすが[切削式ローレット] !
ここまでの費用は
端材等々ガレージに有った物を使っておおよそ \6〜7,000程度でした。
きっと全ての材料を定価で購入しても\10,000程度ですね。
この程度の投資でこれだけの加工が可能になれば最高です。
これで樹脂や木材に埋め込む部材の足付け加工やオーディオのチャンネル、自作工具のグリップ、その他装飾品等々と加工の幅が非常に広がりました。
また、小型旋盤で多少硬い材質や逆に樹脂などの素材へも加工が可能なので用途は無限ですね。 |
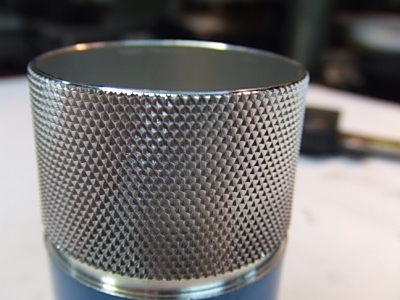 |
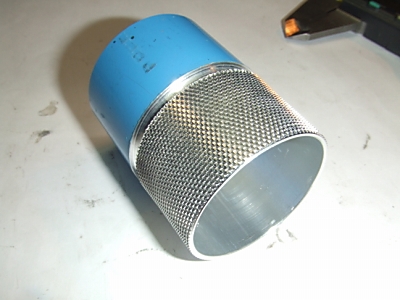 |
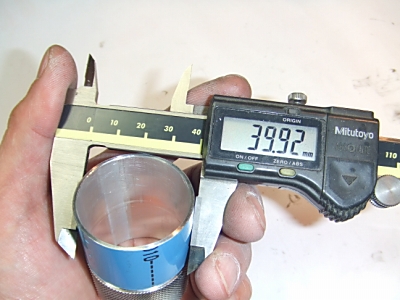 |
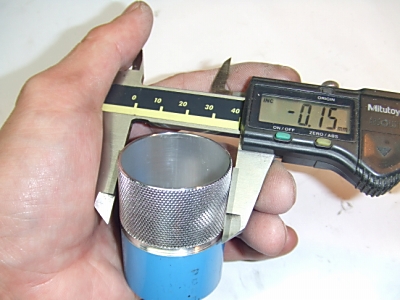 |
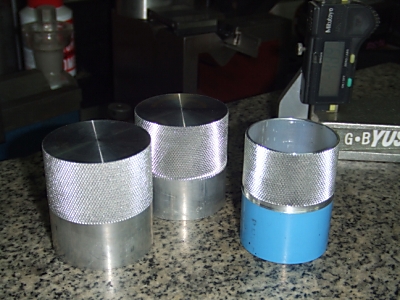 |
今回加工が終了したテストピース(ワーク)です。 |
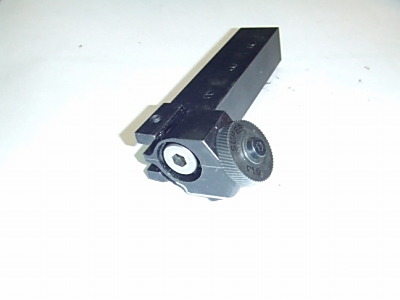 |
ちなみに追加で[平目用の切削式ローレット]も作ってみました。
これも、なかなかの物です。 |
旋盤を使い始めると一度は挑戦してみたくなるローレット加工、小型旋盤ではなかなか難しく敬遠しがちだったでしょうが、今回の[切削式ローレット]で、皆さんの夢が叶い、またひとつ素晴しい作品ができる事と思います。
今まで諦めるしか選択肢の無かった、私とご同輩の初心者の方の一助になれば幸いと存じます。
今回も最後まで、お付き合いありがとうございました。
m(__)m
|
 |
 |