|
|
出力一定の主軸用機械式(ベルト掛け)変速機を自作してみます。
今回は失敗の可能性もありますので、その時はゴメンナサイ (^^ゞ |
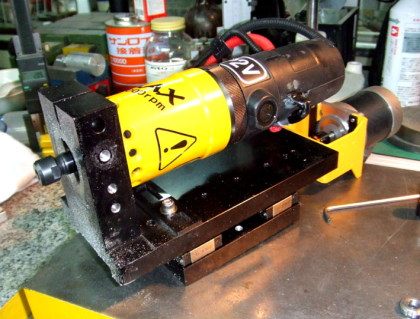 |
【無段変速機の必要性】
現在は主軸に日立のGP2Vというハンド・グラインダーのベアリングを高精度な物に換装し、回転数検出用のフォト・スイッチを取りつけてトライアックで可変速をしています。
30,000rpmまで回りますので細径のミル(刃物)を使用するのには何ら不自由は感じないのですが、太径のミル(5.0mm〜)を使う場合、ワークの材質によっては低速回転域での切削が必要となりトライアックによる可変速では回転数に比例してトルクも減少してしまう為、切削の制限を受けてしまいます。
そこで機械式の可変速の登場となる訳ですが、機械式の変速の場合は一般的にトルクは回転数に反比例し出力一定となりますので
小径刃物の場合 → 低トルク = 高速回転
太径刃物の場合 → 高トルク = 低速回転
切削に対する変速については理想的な特性と思います。
・・と、言う事で何とか主軸に機械式の無段変速機を組み込んで見る事に致します。
但し 0〜100%を機械式だけでとなると難しいので目標は機械式の部分で 0.5〜2 : 1 をカバーしそれ以外の部分を電気式のトライアック若しくはインバーター(定トルク)でカバーし、
結果 0〜2 : 1 をカバーする変速機の自作に挑戦致します。
(^。^)
変速方法としては当初、左上のような可変プーリーとワンウェイ・クラッチを使用したものの構想を立てていましたが、カウンター軸でも10,000rpmオーバーになりますのでワンウェイクラッチがもたない事と構造が複雑になり過ぎ誰でもが作れるわけではなくなりますので、左下のテーパーコーン・プーリーによる簡単な構造にする事にしました。
主軸モーターの回転数を初段の変速で10,000rpmに持って行いけるようプーリー比で調整し、カウンターと主軸の間で可変速をかける事とします。
ファイナル回転数は上記様
5,000〜20,000rpm(機械式変速)
×
0 〜 100% (電気制御)
になるように考えます。
問題はベルトのシフト機構とベルトの耐久性についてなのですが、まぁ〜これから考えるとしましよぅ〜
(^。^)
|
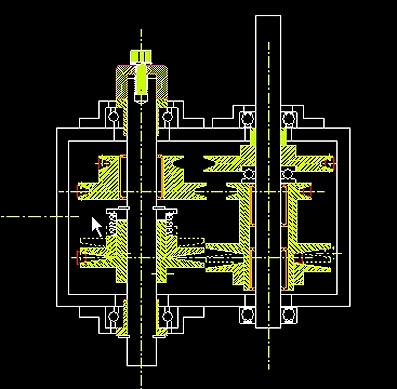 |
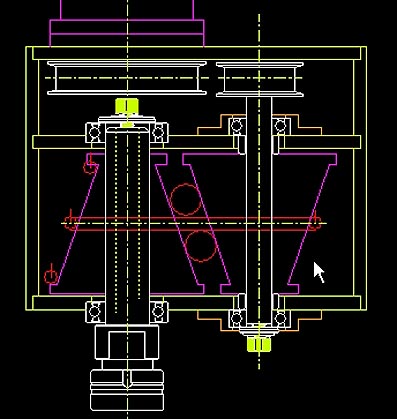 |
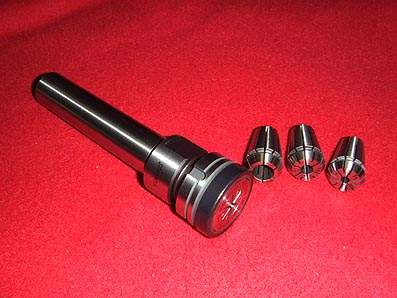 |
【 材料の調達@ 】
《 主 軸 》
まず主軸にするスピンドルですが、取り合えず手元に有ったYUKIWA(ユキワ)のニュードリル・ミル・チャックを使う事にします。
これはストレートシャンクの ST20-NDC10-130で
シャンク径 Φ20mm 適用コレット Φ10mm 全長130mm シャンク長 約90mm の寸法のものです。
精度は、私的に"ソコソコ"じゃないかなぁ〜って思います。 |
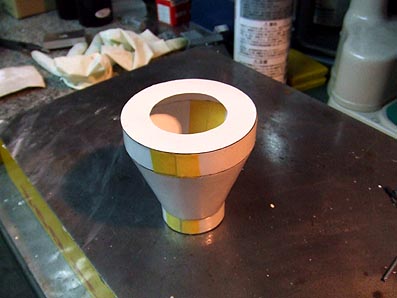 |
【 材料の調達A 】
《 プーリー用アルミ素材 》
Φ80mm × 80mm 程のアルミ素材が必要なのですが、あいにく手持ちの材料が無いのと丸棒からの切削ですと、円柱の削り出しの為かなり切削しなければならないので大まかな形の素材を作る事にしましょう。
取り合えず図面から展開したパーツを厚紙に貼り付け図画工作をしましょう。
次に、その中にFRP成型で使う2液性のポリエステル樹脂を流し込み雄型を一旦つくります。
次にペットボトルの胴の部分から切り出した物を外枠として先に作ったポリエステル製の雄型を中に置き若干湿らした鋳砂を棒などで突き固めながら周りに入れて行きます。
鋳砂は取引先のスパー鉄工所の鋳物部門からもらって来ました。
ヽ(^。^)ノ
・・・・・何をしたいかと言いますと・・・
・・・これからアルミの鋳造をやろうとしているのです。
上手くいったら量産しようかナぁ〜って考えて、それを想定しての事だったりして・・・(^_^)
大よそできたら、ひっくり返して反対側から雄型を抜き取れば雌鋳型の完成です。
奥に写っているのは雄型を抜く前の状態で、引き抜き取っての代わりにボルトを入れてあります。
後はゆっくり自然乾燥をするだけです。
完全に乾燥させずに湯(アルミを溶かした物)を注ぐと湯の高温で発生した水蒸気により巣が一杯できそうなもので・・・
本当は高速回転のプーリーは内部の組成が安定している市販の引き抜き丸棒素材から削り出した方がバランスが良いのですが、ちょっとアルミの鋳造を久方にやってみたかったのです。
ゆえに、完成品がバランス不良であれば丸棒から作り直す事にします。 m(__)m
《 アルミ鋳造 》
後方に見える、不要になったV-Max4のクランクケース(たぶんA2024系アルミ)を炉で880℃程度で溶解させ前述で完成した雌型にいっきに注ぎ込みます。
躊躇していると巣ができてしまいますのでクルリとコーヒー・ドリップの要領で・・・
アルミ素材の選定は対磨耗性と切削加工性を考慮しました。
充分に冷めたのを見計らって砂型を壊せばアルミ原型素材の完成です。
うむぅ〜・・・
(^^♪
まぁ〜この段階までは良しとしましょう。 |
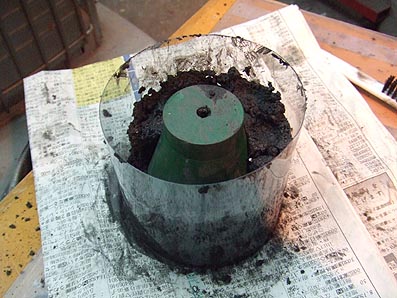 |
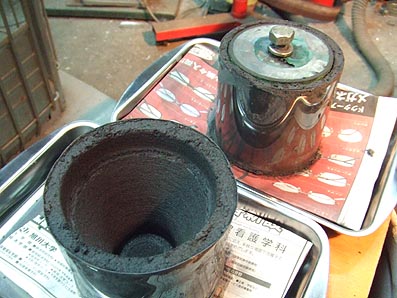 |
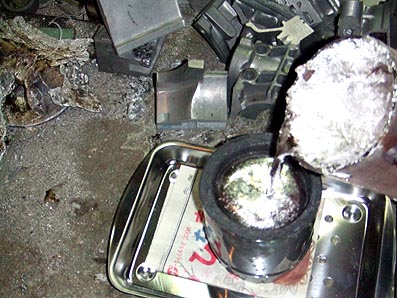 |
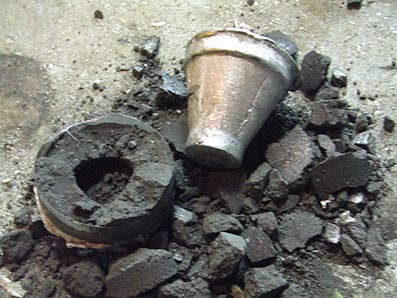 |
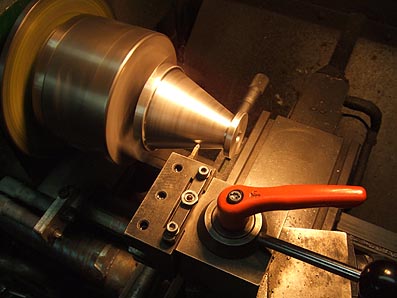 |
《 プリー加工 》
テーパー切削についてはトップスライドの分度器を目安に浅い切込みで一回目送ってみて、ワークのテーパー寸法を測定して角度の微調整を行います。
今回の場合は、横に54.8mm送って19.0mmの勾配になるように調整いたしました。
思いのほか良いできかな・・?
(^。^)
《 軸 穴 加 工 》
軸穴については
@センタードリルで錐芯を付ける。
A何段階に分けてドリルで下穴加工。
Bボーリングバイトで-0.1程度まで仕上げ。
Cリマーで最後に寸法仕上げ。
リマーには充分切削油を付けて作業します。(私の場合アルミには灯油で切削ペーストを溶かした物を使用しています) |
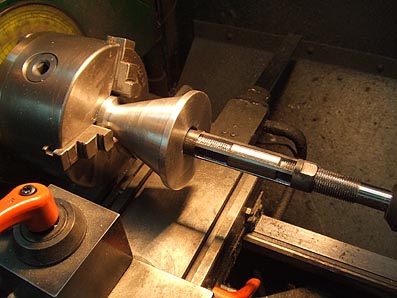 |
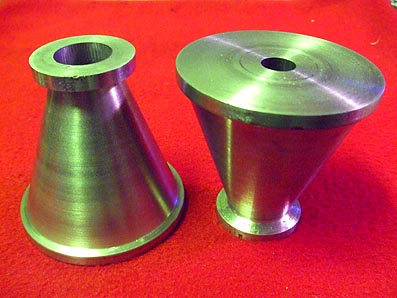 |
《 テーパーコーン・プーリーの完成 》
かなり満足できる仕上がりかな・・・
残す問題は、バランスですね (ーー;)
|
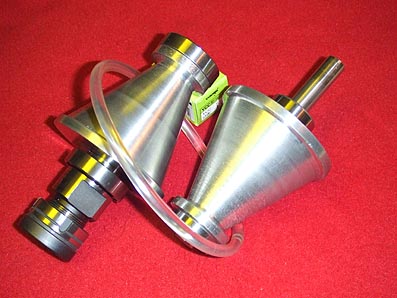 |
《 主軸周りの役者が揃いました 》
主 軸Φ20で、 べアリングは 6904ZZ
カウンター軸Φ12で、べアリングは 6001ZZ
ベルトはΦ6.0のポリウレタン丸ベルトでェ〜ス
後はケースの詳細設計と加工です。
さぁ〜頑張るぞ ! |
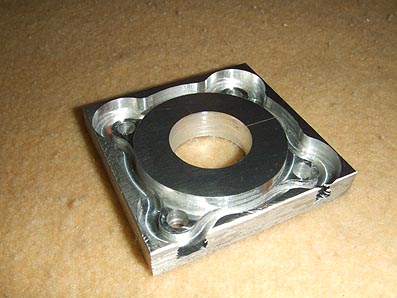 |
《 ベアリングホルダーの製作 》
現行のmini-CNCを使って主軸とカウンターシャフト用のベアリングのブラケットを作ります。
9.0mmの#2000のアルミ板からF=800程度で段付きの切り抜き加工をします。
切削加工が終了したら一度アルミナでサンド・ブラストをかけバリ取りと足付けの下地処理をしたら密着材を軽く吹き付けた後、好みの塗装をします。
オーブンで5分程度焼付けし換装させたら端面等を定盤に貼り付けたペーパーで面研ぎを行います。
左が完成した主軸側のベアリング・ホルダーです。
塗色は私のCNCカラーの黄色にしました。 |
 |
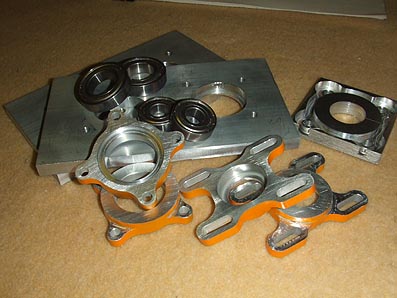 |
《 軸受け廻りの完成部品 》
左が、其々の完成したベアリング・ホルダー関係の部品です。
ベアリングの穴は後からベアリングに合わせて旋盤で寸法公差の調整をしましょう。 |
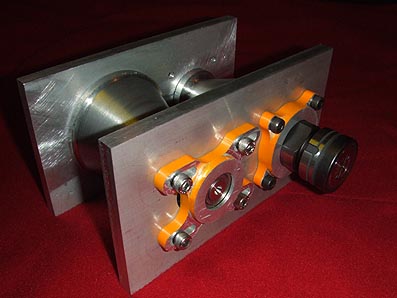 |
《 主軸の仮組み 》
ここで一旦、各主要部品を仮組みして見ます。
なかなか、しっくりとした感じです。
(^。^)
カッチョ、エ〜
カウンター軸のベアリングホルダーについてはベルトの張り調整の為に固定ボルト穴は長穴に加工して有ります。
一番下の画像が真上から見た物です。
なんとなく、これに丸ベルトを掛けると、何だかテーパーがキツ過ぎてベルトが斜めになってしまうような気もします・・・・(^^ゞ
う〜ん・・・・ ここで思案・・
もし、ベルトが滑って斜めになるようであれば無段変速は諦め、テーパーコーン・プーリーの外周に何本もベルト用の丸溝を切って多段変速に変更も必要かな・・?
ただ、変速比の切り替えようのテンショナー兼シフターが付くので現時点では、まだ ???? ?
取り合えず初心貫徹で、がんばろ〜ぅと !
でも、現時点で見る限りは我ながらカッコ良い
(^。^)
でも、何かしらの不安がよぎりますね
(ーー;)
プーリーの傾斜がキツ過ぎない ? |
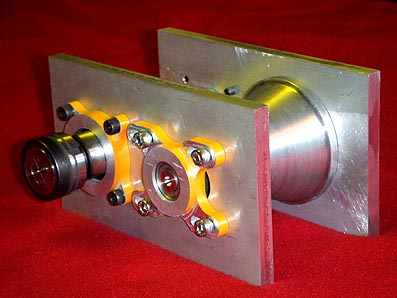 |
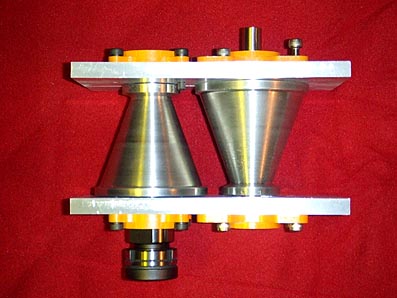 |
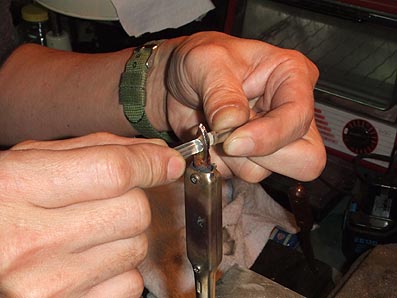 |
《丸ベルトのエンドレス》
Φ6mmのウレタン丸ベルトを熱溶着でエンドレスします。
一般的なのですがコテ先を平らに研いだ半田ごてを使います。
コテ先の両側から単面を押し当て、トロ〜リと溶けてきたらコテから離し両端を厚着し完全に冷えてからはみ出した部分を整形します。 |
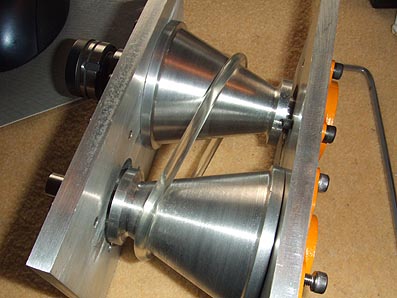 |
【・・・・・ (ーー;) 】
コーンのテーパーがキツかったかな ・・?
ベルトが逃げてしまいますねェ〜
不安が的中・・・かな
ひょっとして・・・し・っ・ぱ・い・・・・
うむぅ〜 (ーー;) |
【 主軸必要回転数 】
ここで、もう一度主軸の必要回転数を考え直してみるとしよう (^^ゞ
ハイスのエンドミルの、いつも行っているドライ切削での条件を再度確認してみる事にしましょう。
ワーク(切削素材)は#2000,#5000のアルミの場合下記条件で主軸の回転数を決定しています。
但し送りについてはZの切り込みを0.15〜0.25mmと浅くして F=400〜1,000mm/miniで切削していたなぁ〜 。
下記条件は刃物径(Φmm)の1/2の切込み量で想定していた・・・ハズ (^^ゞ
刃物の周速(mm/mini)はハイスなので 50〜70m/miniに、超鋼の場合は100〜200m/miniが一般的なはず。
|
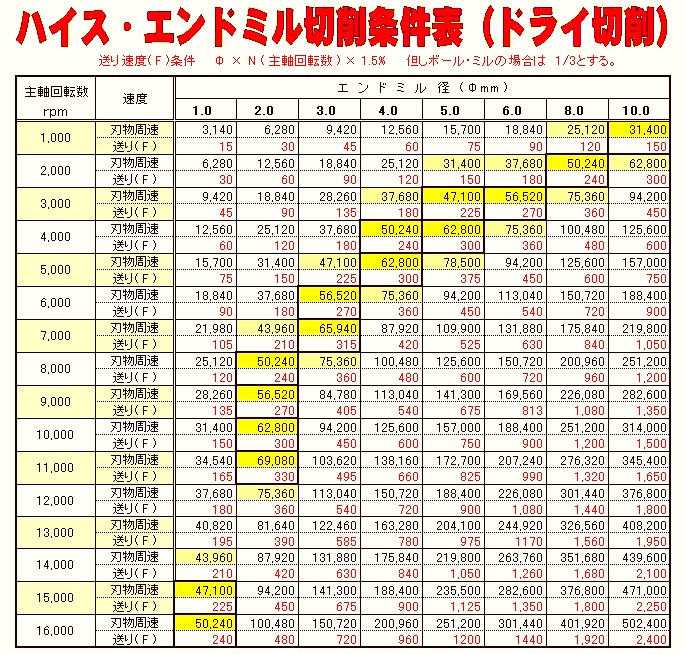 |
いわゆる今までの切削条件を満たすとなると主軸の回転数は 1,000〜15,000rpm程度で軸トルクは
やはり定出力型(トルク=回転数に反比例)が必要って事になるのかな・・・・?
トルク(kgf・m) = 974×出力(KW) / 回転数(rpm) 必要軸動力は ? ?
でも今後、超鋼の刃物を使うとなると、やはり〜20,000rpmは欲しいところかなぁ〜
行き当たりバッタリの私らしく設計と製作が本末転倒になっちゃいました〜
うむぅ〜 ・・・モーターは何を使うかも含めて、再検討します。 m(__)m
|
特 集 失 敗 の 巻 ・ ・ ・ ! |
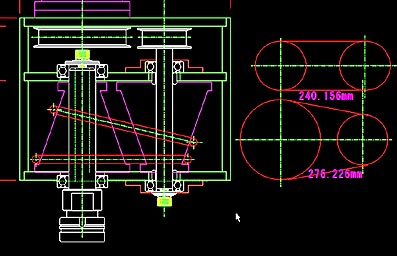
|
【 敗戦の将、チョットだけ語る 】
気をとりなおして、もう一度設計を再検討してみる事にしまし・・・・・・・・・たら
えっ〜 !
プーリーのどの場所でも周長は一定のはずなのに斜め掛けになると周長が短い・・。
設計ではどの位置でも周長は274mmのはずなのに左画像のCの位置で斜め掛けになると、な・なんと周長は240mmだぁ〜 !
なぜ ???? (T_T) なんで ??
でも実際に仮組をすると、どうもこの位置にベルトが居たがるのがわかる。
特に張りを強くするほど、この位置に来たがる。
(ーー;)
張りを弱くすれば改善されるが軸動力の伝達率が落ちてしまう。
やはり、テパー・コーンの角度がキツイのが原因で、ベルトがプーリーに斜めに掛かる楕円々弧の変化と斜めになる接線の変化のバランスの問題だなぁ〜・・・・・ (ーー;)
対策としては軸間距離を出来るだけ大きくして変速切り替えようのシフター兼テンショナーでベルト位置を矯正するしかないのだが、それでは、あまりにも形状が大きくなってしまう。
算術は苦手であるが直感的に考えると、もっとプーリーが長くなくてはならないのだと思う。
|
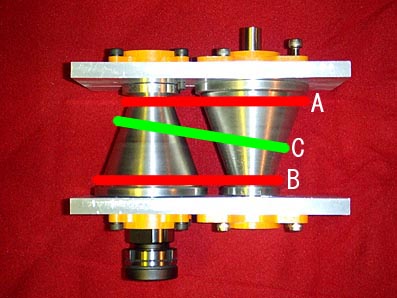 |
【 お 詫 び 】
みなさん期待を持たせたのですが、このような結果に終わりました。
ざ・ん・ねェ〜・ん・・・ ごめんなさい。
m(_ _)m
、・・・と言う事で取り合えず、この特集はやはり失敗に終わりました。
ちょっと充電して又、何か特集を考えますので、今後とも宜しくお願い致します。
|
 |