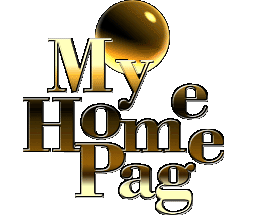 |
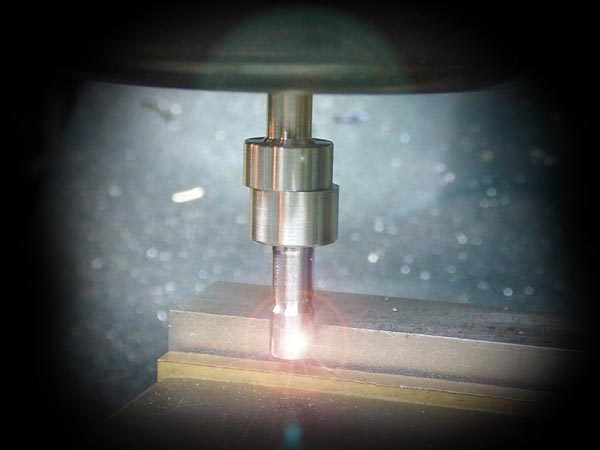 |
みなさん既定材料からの芯出し(原点出し)は、どうされていますか?
一般的に無垢材からの切り抜き切削であれば特に適当でも問題は無い場合も有りますが、既定材からの外形加工切削においては必ず何かしらの方法で原点を出さなければならず、何かしらのチェッカーを使わなければなりません。
そこで登場するのが[芯出しバー]で、各メーカーによって色々な呼称があります。
[芯出しバー] フジツール
[センタリングバー] フジツール
[スタイラスセンター] SK
[アキュセンター高精度芯出しバー] 大昭和精機(BIG)
基本的構造は、どれも同じで非常に簡便な操作で超精密な位置出しが可能です。
角物材料を例に取れば、主軸に[芯出しバー]を銜えさせ上下の接合面を若干ずらしておき、低速回転(600〜800rpm)で回転させながら角物のXもしくはYの基準面にしたい端面にゆっくりと先端を当てて行き材料に触れると[芯出しバー]の偏芯が抑制され真円回転となってゆきます。
その段階で、慎重にもうひと送りすると『カクッ』と上下の接合面が[ズレ]を起こします。
この点が[真にバーが材料に触れた位置]となるわけですから、後は[芯出しバー]の接触子の直径の1/2を再度追送りすれば、その主軸中心の真下が、その材料の一方の面[真の端面]になりますので[カウンターを"0"セット]すればよいわけです。
この単純な作業をX,Y両面について行えば誰でも簡単にX=0,Y=0の原点出しが高精度で実現できると言う事です。
が・しかしmini-CNCにおいては主軸コレットの最大寸法がΦ6.0mmという機械が多いにも係わらず〔芯出しバー〕について現在Φ10.0mmの物しか残念ながら市販されていません・・・・(^_^;)
で・mini-CNC愛好家のみなさんの為にΦ6.0mmの物を作ってみる事にしました。
要点さえ押さえれば確実簡単にできますので是非トライしてみて下さい ネ (^。^)
|
【 構 造 】 |
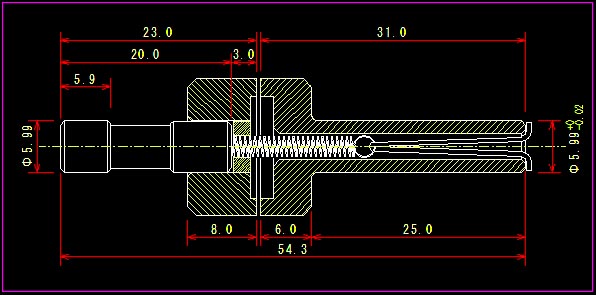 |
これから作る物の構造は上図のように、いたってシンプルなものです。
シャンクを持った2個の円盤状の物を内部のスプリングで面を引き合わせただけです。
市販製品は両方のシャンクが中空になっており、その中にスプリングを通してあるようで材質はSK材等の工具鋼などの焼き入れ品ですが、今回は耐磨耗性を考慮し接触子側のシャンクはハイスか超硬で作ろうと思います。
性能(精度)に影響のある部分は円盤状の接合面の平面度(面粗度)と、それに対するシャンク部分の直角度および接触子部分の真円精度と直径精度だけです。
あとは結構アバウトでも、ソコソコ高精度な物ができると思います。
・・・・・・スミマセン (^^ゞ
寸法が抜けていました。 円盤(接合面)の外形(直径)は約Φ12mmです。
|
|
【 材 料 】 |
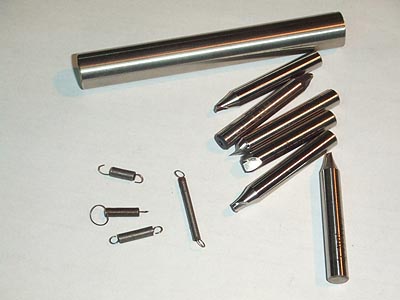 |
【 材 料 】
材料は、何と言って特殊なものはありません。
折れて使えなくなったΦ6.0mmシャンクのエンドミルとΦ12mmのSUS丸棒。
後は外径Φ2〜3mm程度のスプリングとΦ6mm程度の真鍮丸棒の端材 |
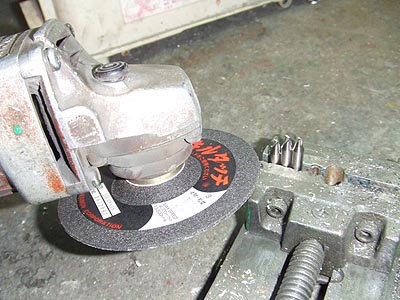 |
まずエンドミルのシャンクを必要長さに切断します。
長さは好みですが今回は20mmにしました。
ハイスのエンドミルでしたらサンダーなどで簡単に切れます。
超硬の場合は切れ目を付けてハンマーで叩いて折れば良いでしょう。 |
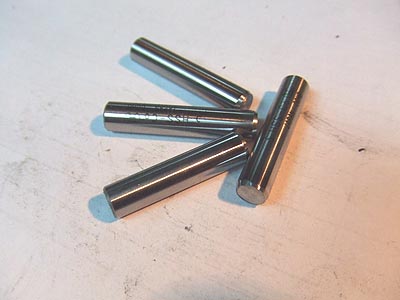 |
切断面をグラインダーなどで整えておきます。
後で切断面方向から圧入しますので角の面取りも忘れずに
ちなみにOSG社のΦ6mmシャンクのエンドミルの径は Φ5.98mm〜Φ5.99mmでした。
これが微妙に丁度良いサイズです。 |
|
【 加工前の機械の調整 】 |
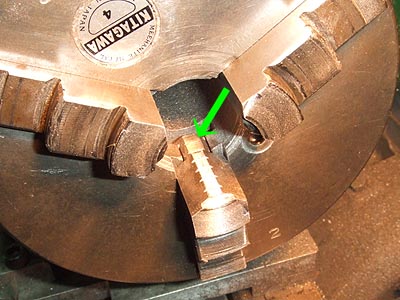 |
[裏技]でも何でも無いのですが私の場合、三つ爪旋盤加工で細かな芯出し作業が面倒ですのでスクロールチャックの爪の調整を定期的に行っています。
特に今回のような精密な加工する前に機械(旋盤)の調整をしておきましょう。
今回は簡便に作る為に、何所にでもる三つ爪スクロールチャックを使用します。
私の場合、チャックの爪は奥の方をグラインダーで削って有ります。 |
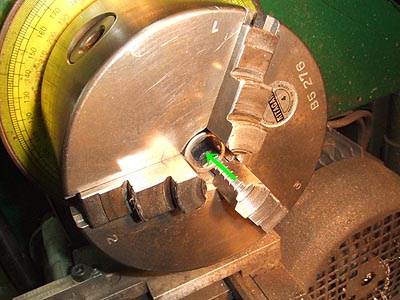 |
次に爪の奥にボックスレンチのコマなど適当な直径の物を銜えておきます。
これは重要です。
これを省略しますと何の意味も無くなります。
(^_^;)
|
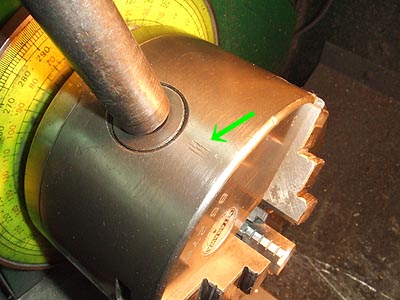 |
旋盤を使うに当って常識的な事ですがマークの有る決められた位置で常に締め付けを行います。
大径の物の場合は均等に各位置で締め付けた後、最後にもう一度、この所定の位置で強く締め付けます。
私の機械のKITAGAWAのチャックの場合3本線のマークが打ってあります。 |
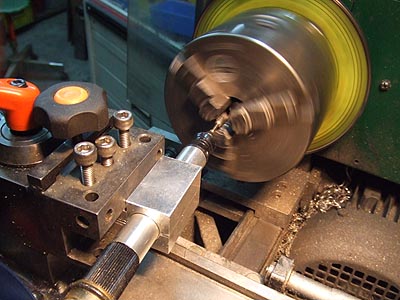 |
それでは、いよいよ爪の内面研削をしましょう。
エアーリューター(ハンドグラインダー等)にダイヤモンド砥石を付けチャックを回転させ慎重に送ってゆきます。 |
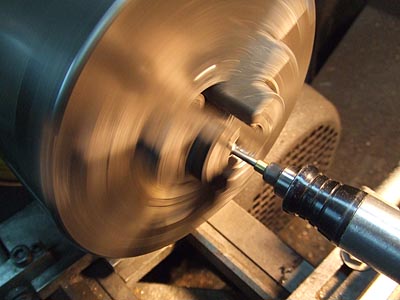 |
これも好みですが旋盤のチャックは600rpm〜1,000rpm程度が良いでしょう。
グラインダーの方は20,000rpm程度で回しています。
チャックの入り口から奥まで満遍なく何度も切り込みを変えて送り研磨しましょう。
焼きの入っていないチャックでしたら超硬のボーリングバイトで削ってもOKでしょう。 |
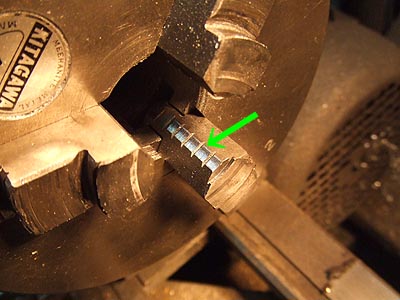 |
このように綺麗に研磨できました。
これで何を銜えても必ず芯がでるはず。 ヽ(^。^)ノ
爪の奥を削ってある訳が分かったと思いますが、爪を研削する場合既定の締め込み状態で研削しないとガタガタで精度が出ない為に何かを銜えるわけですが当然その部分は研削できませんので予め削って低くしてあるのです。 |
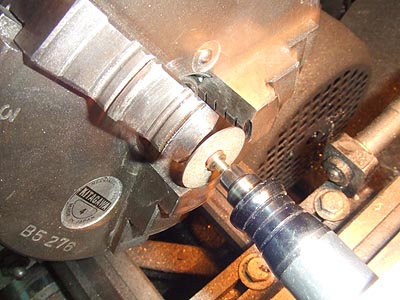 |
久しぶりに爪研削の段取りをせっかくしましたので爪先端も整えておきましょう。
これにはダイヤモンドディスクを使いますが、ホームセンターで数枚で数百円と言う安価な物でも差し支えありません。
この部分は若干大き目に、そして深さは1.0mm〜2.0mm程度の掘り込みで良いでしょう。 |
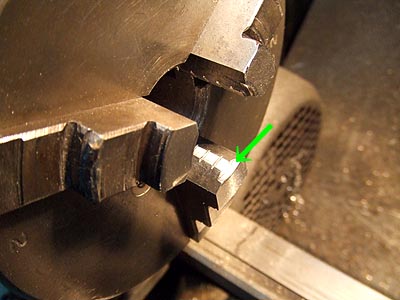 |
矢印のように段差ができればOKですが、奥角の部分は逃げを取っておいた方が材料を銜えた時に材料の角で浮き上がらず使い良いと思います。 |
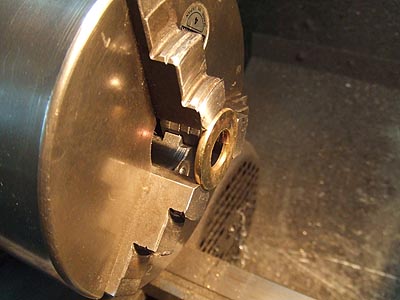 |
これで、ちょっとした加工であれば芯出し不要で高精度なセットが可能になります。
特に左画像のようにワッシャーなどの薄物を銜える時など格段に威力を発揮します。
基本的には、これでチャックを取り外さない限り、材料の反転加工などでも確実に精度がでる・・・ハズ・・(^。^)
ですよ・・・ね (^^ゞ |
|
【 加工・その@ 】 |
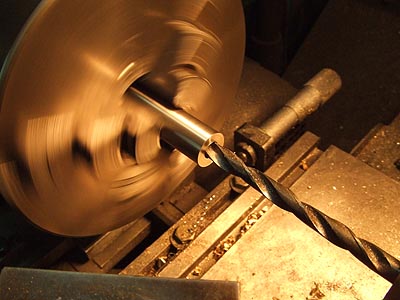 |
【 ディスクの製作 】
それでは、チャックの高精度調整(修正)もできましたので、いよいよ[芯出しバー]の製作にかかりましょう。
Φ12mmのSUS丸棒から切り出します。
端面を整えた後、センタードリルで中心に錐揉みを入れΦ4.0mm 次にΦ5.9mmのキリを使い二段階で中心に穴を開けます。
切削油は十分に塗布してください。 |
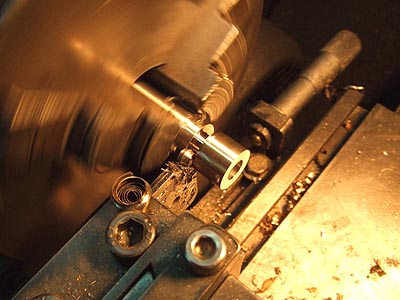 |
次に8mm〜9mm程度の長さで突っ切りバイトを使い切り落します。
片方の端面さえ整えてあれば別に鋸で落しても構いません。 |
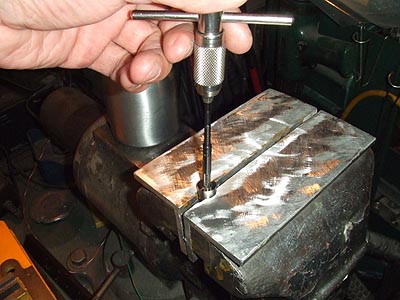 |
上で切り落したコマの中心の穴を整えます。
アジャスタブル・リマーを使いΦ5.96mm程度に仕上げましょう。
リマーは入れる時も抜く時も必ず時計方向で切削油をタップリ使い回転させながら行う事が肝心です。
逆転させて抜くと歯が欠ける場合があります。 |
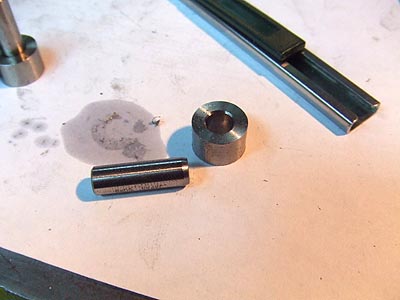 |
できたコマ(ディスク)と先に作ったシャンクです。 |
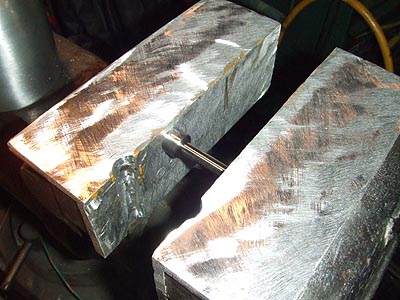 |
【接触子の組み立て】
Φ5.96mmのディスクの穴にΦ5.98mmのシャンクを圧入します。
プレスが無ければ万力などのバイス類で締め込んでもOKです。
但し、口金には必ずアルミ等で素材保護の為の養生をしておく事。
注意 : 一気に入れず、少しづつ挿入し最後3mm程度は必ず残しておく事。 |
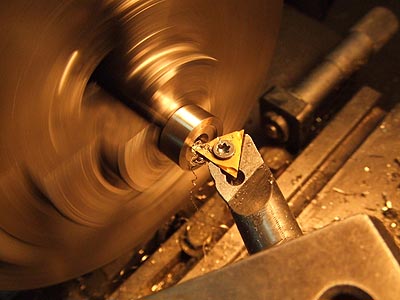 |
接触子側のディスクを整えます。
この場合は接触子(エンドミルのシャンク)を基準に加工してゆきますので爪を整えたチャックにしっかりと銜えます。
まずディスク内面を0.5mm〜1.0mm程度の深さで掘り込みます。
外周のツバ幅は1.0mm程度で良いでしょう。
今回はボーリングバイトの刃先で掘り込みました。 |
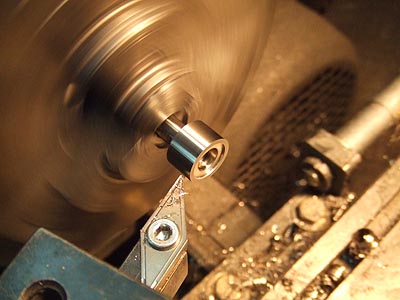 |
次に上記同様、接触子(エンドミルのシャンク)を基準にディスクの外周を整えます。
多分0.1mm〜0.2mm程度削れば真円となるはずです。
当然、端面も慎重に整えて下さい。
これで接触子(エンドミルのシャンク)に対する、おおよその直角は出るはずです。 |
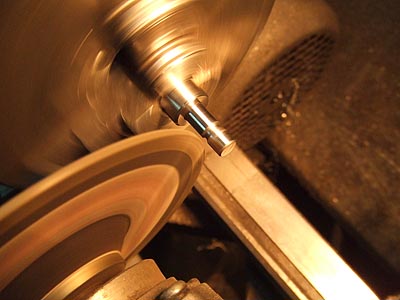 |
接触子に境目をつけておきましょう。
銜え方を反転させ爪の先端で銜えます。
次にディスクサンダーを回転させながら当てます。
これで綺麗なクビレを付ける事ができるはずです。 |
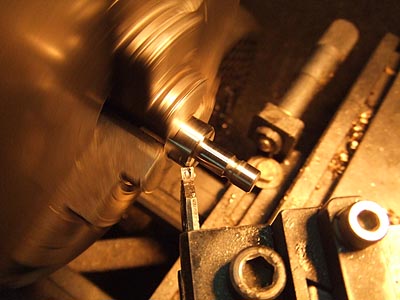 |
ついでですから面取りも行っておきましょうか。 |
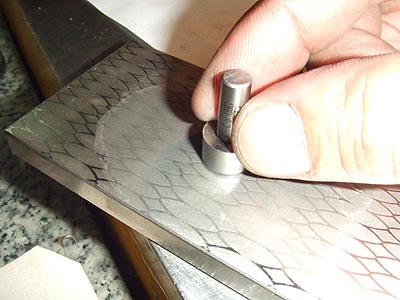 |
それでは完成した接触子側のディスク面を細目のダイヤモンド砥石などでラッピングし切削目を殺しましょう。
切削オイルを塗り、くれぐれも慎重に・・・・
これでディスク面の直角が出るはずです。 |
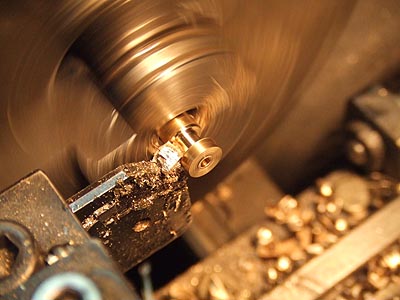 |
【スプリング固定金具の製作】
Φ6.0mmの真鍮丸棒の中心にΦ2.6mm程度の穴を開け外周をΦ5.95mm程度に整えた物を2.5mm厚さ程度で切り落します。
寸法精度は特に気にする必要はありません。 |
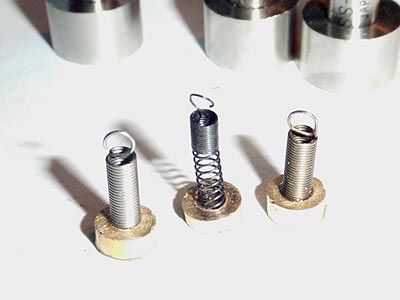 |
上記でできた真鍮のコマの中央にスプリングを入れ瞬間接着剤で固定しましょう。
接着前には必ずパーツクリーナーなどで脱脂をして切削油などを除去しておいて下さい。 |
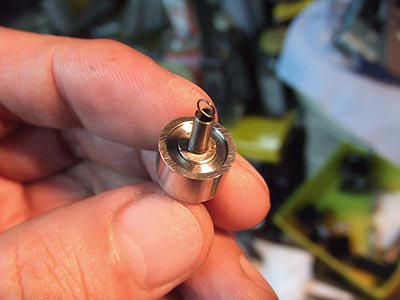 |
先程作っておいた接触子側のディスクの中央に上記で作ったスプリング付のコマを瞬間接着剤で固定しましょう。
これを入れる為に圧入の時、若干残しておいたのです。
ハイスや超硬の端面にΦ2.5mmの穴を開けれる方は、この工程は不要ですが・・・・(^^ゞ |
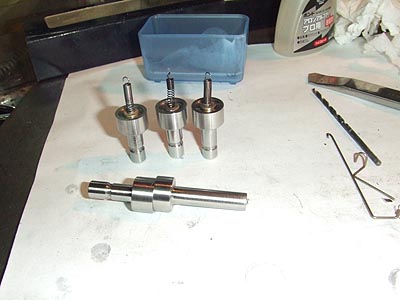 |
・・・・こんなんで片側(接触子側)が3個ほど完成しました。 |
|
【 加工・そのA 】 |
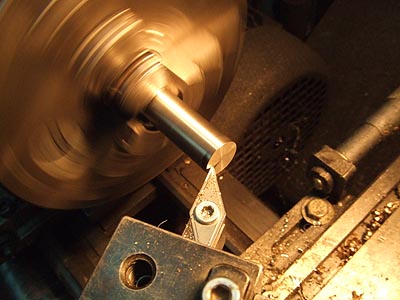 |
【 シャンク側の製作 】
それではシャンク側を作りましょう。
材料はΦ12mm長さ40mm程度のSUS丸棒から削り出します。
まず端面を整えましょう。 |
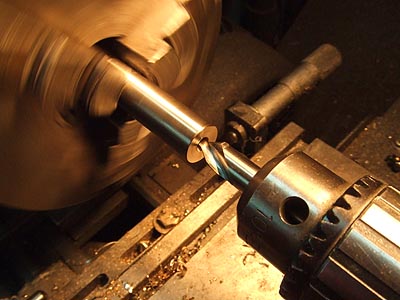 |
次にセンタードリルで揉み付けを行います。
切削油は十分に (^.^) |
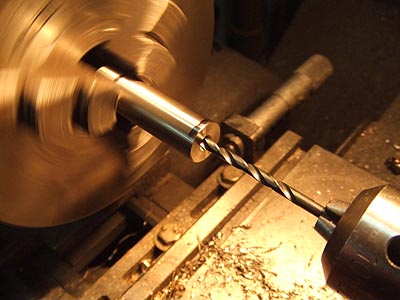 |
Φ3.0mmのキリで一気に貫通穴を開けましょう。
・・・と・・言っても相手はステンレスですので充分な切削油を塗布し慎重に抜き差しを繰り返し切子を排出しながら行いましょう。 |
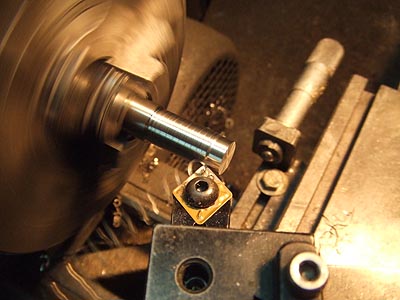 |
コレットに銜えるシャンク部分を削りだしましょう。
Φ6.2mm程度までは荒取で良いでしょう。
長さは約25mm程度でOKです。 |
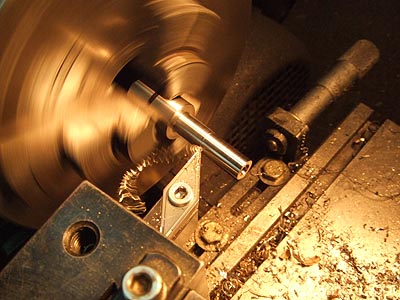 |
バイトを交換して仕上げ切削を行います。
0.02mm〜0.05mm程度の切込みで仕上げてゆきます。
切削油は充分に塗布しましょう。
最終仕上がり径はΦ5.99mm(+0/-0.03)を目標に |
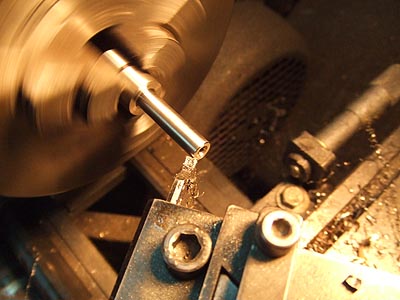 |
ついでに・・・・面取りも、しちゃいましょう
(^.^) |
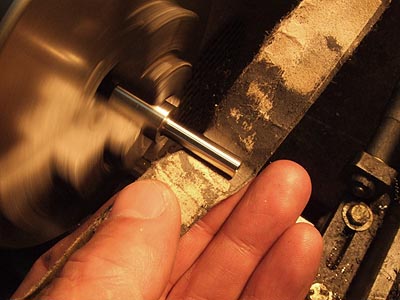 |
目を潰したサンドペーパーで切削目を消します。
回転に合わせて左右に移動させると綺麗なクロスハッチができます。
最後のバイトの切り込みが0.02mmだとしたら、これでその分の0.02mmのバイトが残した[山]を落してしまいますので切削終了寸法は、その分を見込んでおきましょう。
いわゆる仕上がり寸法より0.02mm程度太目に、そして最後の切り込みは同量の0.02mm程度で最終仕上げっちゅう事で。
切削目は使用中、すぐに磨り減って落ちて行き径が細くなりますので必ず、このように目を殺して寸法が出るように工夫してください。
(本来はヘールバイトなどで仕上げるのですが) |
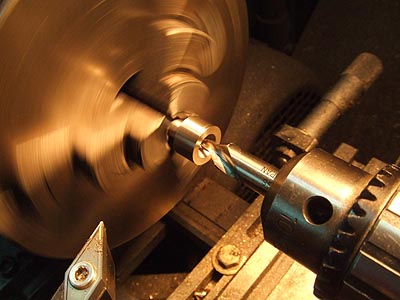 |
次に接触子側と同様にシャンクを基準にディスクを仕上げてゆきます。
冒頭のチャックの爪の修正により、このようなトンボ(反転)加工による銜え直しでも加工精度は良好なはずです。
こちら側は、まずセンタードリルなどで荒取をして下さい。
こちら側(シャンク側)はスプリングが動かなければなりませんので中を広目に掘ります。 |
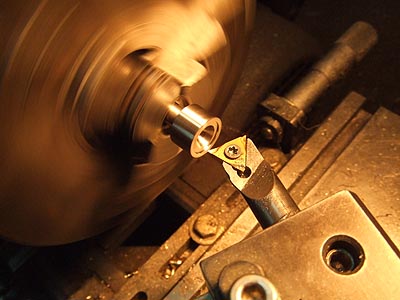 |
接触子側と同様に外周とディスクの端面を慎重に整えます。
外周については接触子側のディスクの直径を実測し、それに合わせて同一の直径として下さい。
|
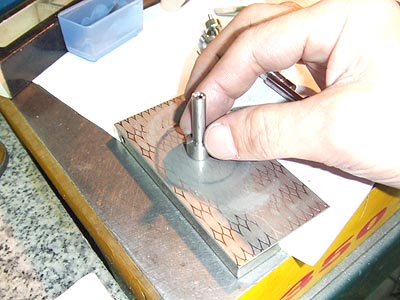 |
こちらも接触子側と同様の作業になりますがディスクの端面をラッピングして整えましょう。
これで、機械加工は無事終了です。
ヽ(^。^)ノ |
|
【 組 み 立 て 】 |
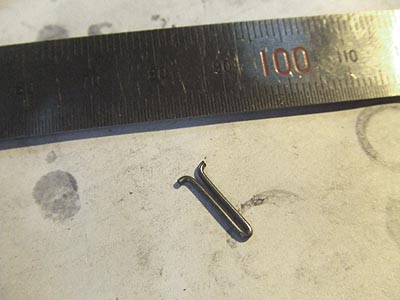 |
【 組 み 立 て 】
Φ0.5mm程度のピアノ線などで左画像のようなスプリング固定金具を作っておきます。 |
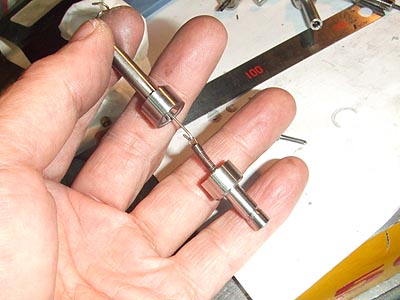 |
シャンク側から先端をフック状にした針金でスプリングの先端を引っ掛け引き込みます。 |
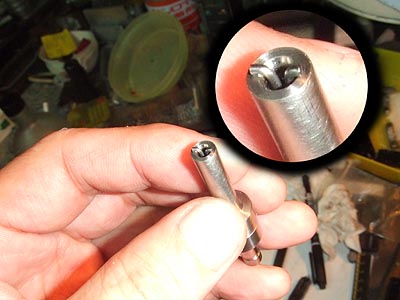 |
引き込んだら先程作ったスプリング固定金具を通しシャンクの中に落とし込めば完成です。
スプリングのどちらかの突端は、このようにフリー(より戻し)にしておかなければ長く使っている間にスプリングが捻切れてしまいます。
また、このような仕組みにしておけば組みあがった後に、どうしても再調整が必要になった場合でも簡単に分解する事ができます。 |
|
|
【 調 整 】 |
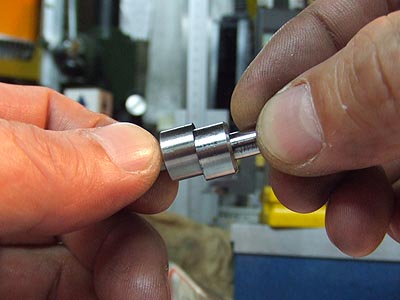 |
測定器の命・・・・《精度》を吹き込みます
非常に重要な作業です
さて・・と・・
それでは精度良く仕上げる為に調整をしましょう。
いくら旋盤のチャックの内面を生爪のように研削したからと言って完璧に誤差ゼロとはならないでしょう。
一番重要な部分はディスクの摺動面で、合わせた時に『ピタ〜』って吸い付くような面精度(面粗度)が必要ですしシャンクとの直角精度も限りなく良くなくてはなりません。
・・・・・が、そんな加工ができる機械を持っていませんのでシンプルかつ確実な方法で精度を上げましょう。
それでは、まずディスクの摺動面(合わせ面)に少量の切削液を垂らしておきます。 |
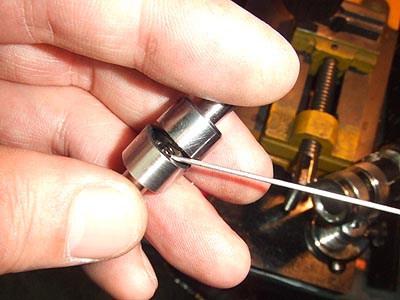 |
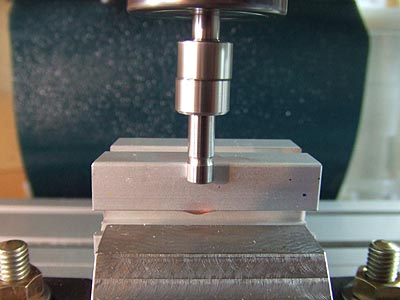 |
CNCのコレットに[芯出しバー]を銜えさせ通常の使い方のように適当なワークに当てます。
主軸の回転数は600rpm程度が良いでしょう。
またワークの接触子が当る面には適当量のオイルを塗布しておきます。
ワークに接触子が当りディスクがズレた状態で一晩ほど(12時間程)回しておきます。
こうする事により、お互いのディスク摺動面(合わせ面)が[成りに]ラッピング(摺り合わせ)され面精度(面粗度)も良くなり、且つシャンクに対する直角度も必然的にでてきます。 |
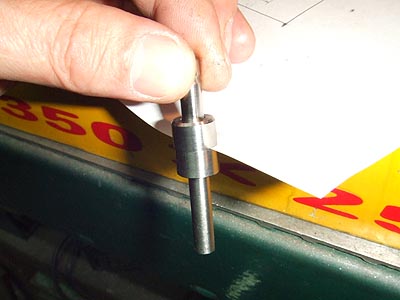 |
ディスクの摺動面(合わせ面)の調整が終了しましたら今度はパーツクリーナー等で洗浄し、新たにオイルを塗っておきましょう。
左画像のように紙を挟めて扱いても良いでしょう。
多分、見違えるほどの面精度(面粗度)が出て[ヌル〜]っとした吸い付くような感じに仕上がっている事と思います。 |
|
【 精 度 試 験 】 |
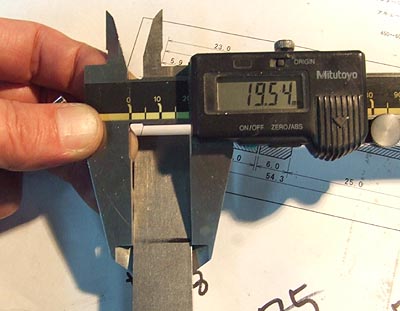 |
【 精度試験(評価試験) 】
それでは、いよいよ完成品の精度試験をしてみましょう。
いくら綺麗に仕上がっても、その精度が出いなければ測定器とは言えません。
と・言うか測定誤差が既知であれば実作業において、その値を補正すればよい訳ですから必ず精度試験は行いましょう。
まず測定試験には既知の寸法のワークを用意いたします。
4面加工した角棒を今回は使います。
まず適当な位置(中央)にマジックでマーキングし、その部分の幅を測っておきます。
画像のように
ミツトヨデジタル・ノギスで19.540mm
ミツトヨマイクロメーターで19.565mm でした。
一応マイクロメーターでの測定値を採用し
ワークの幅は19.565mm に決定 |
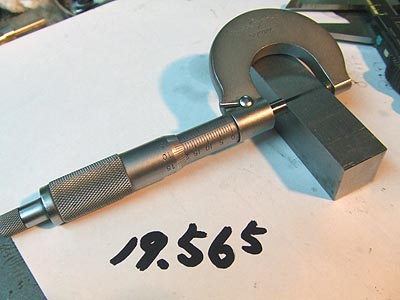 |
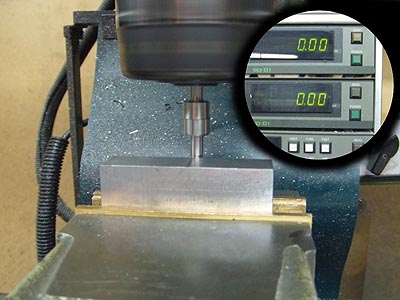 |
それでは上記の既知の寸法のワークをバイスにセットし奧側の面を[芯出しバー]で測定し基準面としましょう。
よろしければミツトヨのデジタルスケールのカウンターを"0"セットします。
画像では上から2段目のカウンターがY軸です。 |
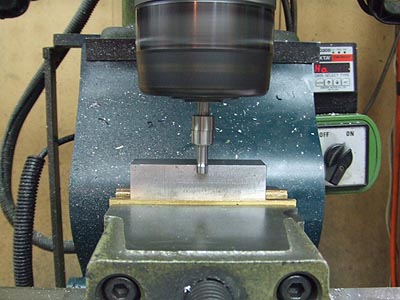 |
次に主軸は持ち上げずに左右にかわして[芯出しバー]を手前に持ってきます。
主軸(Z軸)を持ち上げない理由はテーブルもしくは主軸の上下によりコラム等の遊びで誤差が出る場合があるからです。
一旦、手前にきた[芯出しバー]を送り手前側の端面を測定し、その時のカウンター値を読み取ります。
25.54mmでした
この一連の測定は数度行い再現性を確認しましょう。
後は、この[芯出しバー]により計測した値から接触子の直径の1/2×2(前後測定の為)・・いわゆる直径分を差し引いて、先程実測した既知の寸法のワークの幅19.565mmと比較すれば良いわけです。
[芯出しバー]による測定
25.54mm-Φ6.0mm=19.54mm
実寸法との差異
19.565mm-19.54mm=0.025mm
[芯出しバー]ではワークの前後を計っていますので誤差は2倍でますので1/2にしましょう。
[芯出しバー]の精度
0.025mm/2=-0.012mm(-12μm)
すばらしい〜ぃ・・・・・ヽ(^。^)ノ
|
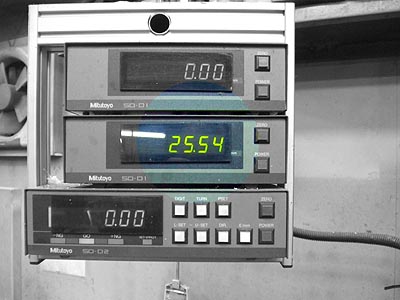 |
【評価の結果】
上述のように精度は-0.012mmと言う結果がでました。
が、しかし・これをどうとらえるかによって・どうとでもなる問題でしょう。
接触子の直径をΦ6.0mmと仮定しての計算ですので、より高精度を要求するのであれば直径を実寸のΦ5.975mmと考えて測定すれば良い事です。
(実際のエンドミルのシャンクの径は実測でΦ5.98mmでしたので言い換えればピッタリの精度が出ている事になりますが・・・・(^^ゞ )
いずれにせよ通常の使用に当っては分かり易く、Φ6.0mm(3.0mmのオフセット/精度12.5μm)、超精密な加工の場合はΦ5.98mm(2.99mmのオフセット/精度2.5μm)という事で使用する事にします。
しかし・ながら検証機器の精度の問題もありますが、Φ6.00mmピッタリのシャンクを使っていれば誤差0の[芯出しバー]が、できていた・・・・の・・・・・(@_@;)
我ながら恐ろしい結果が出てしまいました。 (^^ゞ
|
|
【 完 成 】 |
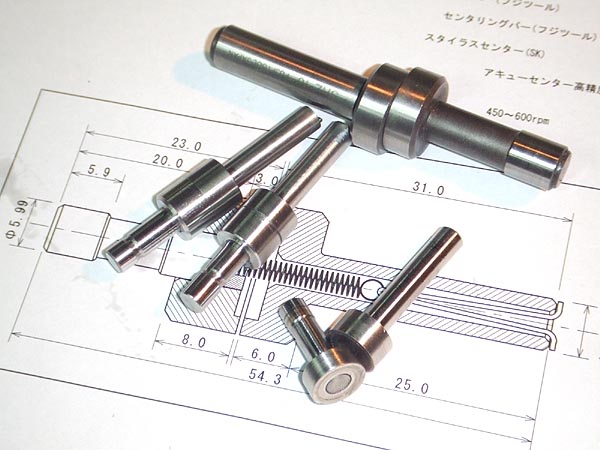 |
完成しましたΦ6.0mmの[芯出しバー]です。
右手前で2分割になっている物は以前に作ったスプリングを使わずに[ネオジ(希土類磁石)]を使ったもので樹脂や非鉄金属での使用には精度的にも満足しているのですが、鉄材で使いますと、磁石なものですからくっついてつかえません・・・・・・(^^ゞ
奥は市販品のΦ10.0mmシャンクの物で精度は2μm程度で、明らかに大きさが違うのがわかります。
|
|
【 芯出しバーの使用例 】 |
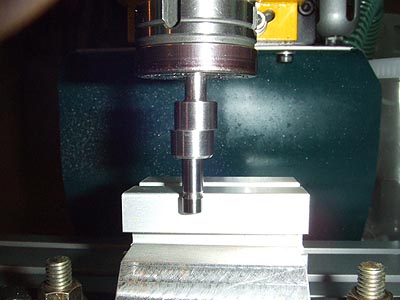 |
[芯出しバー]の使用方法は冒頭でも記載しましたが再度使用方法の一例をご紹介いたします。
アルミ材の手前端面をY軸の"0"原点とする場合
@[芯出しバー]のディスク面を手で若干ずらし主軸を600〜800rpm程度で揺動回転させながらワークに接近させてゆきます。
側面から見ても分かるように、[芯出しバー]の接触子部分は、まだワークに触れていません。 |
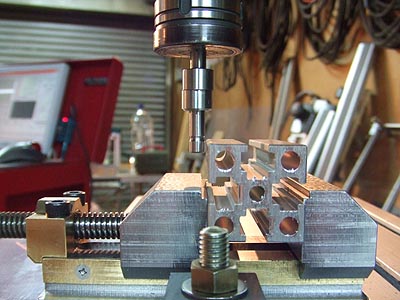 |
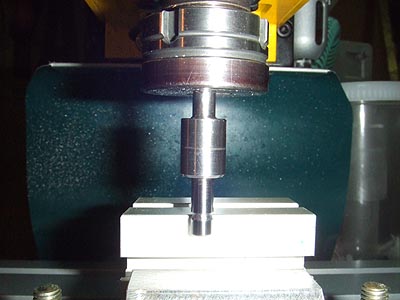 |
A慎重に(徐々に)接近させてゆき接触子がワークの端面に触れ始めると、[芯出しバー]の揺動回転は徐々に抑制されてゆき、ある一点で『ピタッ』と上下が揃った真円運動になります。 |
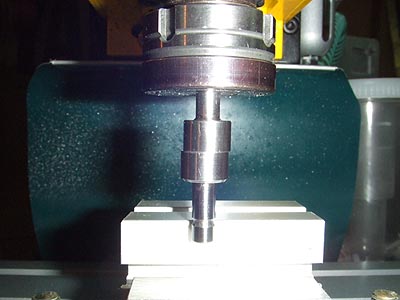 |
ここからが重要です
B上記の状態から慎重に(機械送りの最低ピッチ)で、もう一送りを加えると、『カクッ』とディスクの合わせ面がずれます。
0.001〜0.01mm程度の送り量になると思います
この状態で、送りをもし戻せば上記と同じように『ピタッ』っと上下のディスク同士が合い真円運動に戻ります。
側面から見て分かるように、この『カクッ』っときた状態がワーク端面に接触子が[真]に触れた状態です。
すなわち[基準面]が、このような簡単な操作で決定できるわけです。
ヽ(^。^)ノ |
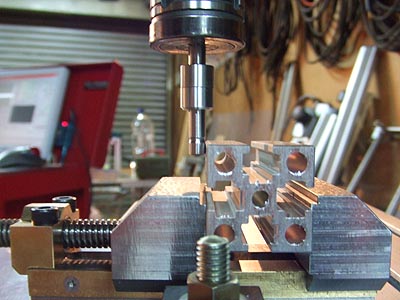 |
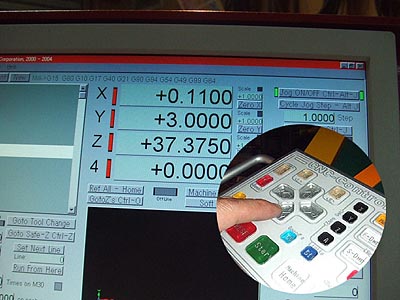 |
C次に主軸(Z軸)を適当な位置まで上昇させます。
[芯出しバー]とワークの干渉がなければ、[芯出しバー]の接触子の1/2(今回はΦ6.0mm×1/2=3.0mm)さらに移動させます。
mini-CNCの場合はMachのカウンターでも良いでしょうしスケールの付いてない汎用機でしたらハンドルのインジケーター・ダイヤルを頼りに送ります。 |
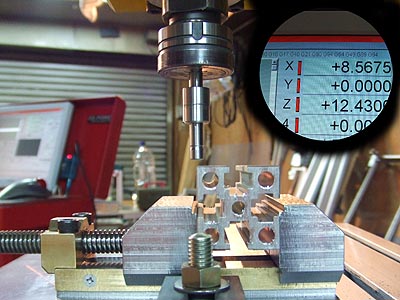 |
D側面からみて分かるようにワーク端面の上部真芯に主軸中心がきていますのでスケールもしくはカウンターのY軸を"0"セットしましょう。
あとは、同様にX軸の芯出しも行い左下隅をX=0/Y=0の原点とします。
このままプログラムスタートしても良いですし、また原点を好きな位置に設定しなおしても良いでしょう。
手動での切削であれば、このようにして端面(基準面)から、いくらの位置からの切削とか・・・・の加工になる事でしょう。 |
|
【 使用例動画 】 |
それでは完成試験の動画をご覧下さい 画質がイマイチで m(__)m
最初、ディスクの合わせをずらしてワークに送っていっていますので揺動していますがワークに接触してゆくと徐々に真円運動に変わり、さらに送ると『カクっ』てずれます。
上記の一例と合わせてご覧下さい。
|
 |
と・言う事で、今回の【特集】も無事完結する事ができました。
稚拙な特集に最後までお付き合い戴き深謝申し上げます。
m(__)m
本[芯出しバー]の製作が初心者の方をはじめ趣味の愛好家の方の一助となれれば幸いです。
|
 |
 |